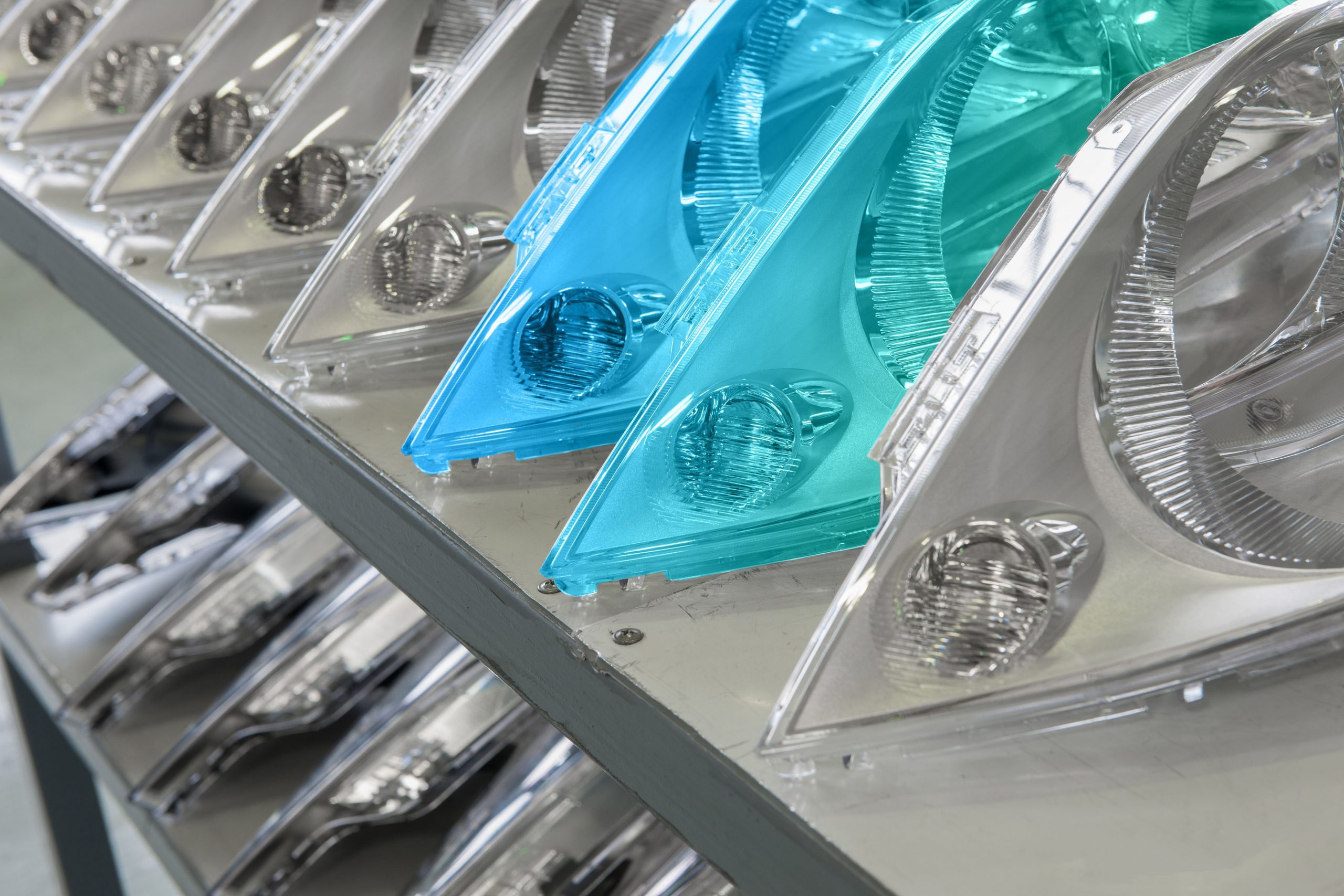
Are you in the automotive industry? Keep reading for a quick overview of what APQP is, the benefits of utilizing it, and the 5 pillars of implementation.
What is APQP?
APQP (Advanced Product Quality Planning) is a structured process with an emphasis on customer satisfaction. It’s the assurance of quality and performance through prevention and detection controls. The major reason the process was put into place was to make sure that the voice of the customer was clearly understood. APQP also helps translate the Product Requirement Specifications (PRS), which include all technical specifications and special characteristics.
APQP is used by companies that are compliant with IATF16949, formally known as ISO/TS16949. IATF16949 is the automotive Quality Management System (QMS) that was created to synchronize assessment and certification systems worldwide in the supply chain. IATF16949 identifies the need for continuous improvement, defect prevention, and reduction of variation and waste. Please note that IATF16949 is an independent QMS standard that is aligned with the requirements of ISO9001 but cannot be implemented as a stand-alone system. The supplier must supplement in conjunction with ISO9001.
APQP heavily focuses on risk, whether that be during new product introduction or during product or process change. In manufacturing, we need to approach all actions with risk-based thinking. If you knew that the outcome of that short shot could mean a deadly car accident due to part failure, would you want to increase your prevention and detection controls? Absolutely! APQP helps us do that.
The Benefits of APQP
Utilizing APQP comes with many benefits, some of which include:
- Promoting early identification of change
- Avoiding late changes by anticipating and preventing failure
- Multiple options for mitigating the risk when found earlier
- On-time quality product at the lowest cost
- Higher capability of verification and validation of a change
- Improved collaboration between Design of the Product and Process
- Lower cost solutions selected earlier in the process
- Lessons learned for future usage
- Helps direct resources to what is truly important
Being able to identify and implement change early on in the process lowers the cost and time involved to make the change. The below image shows what the impact of a change early on in a part design can do for a product launch. The sooner a change is made, the higher the impact and the lower the cost. One of the biggest risks in late changes is a delay in the time to market, which can be detrimental to a project.
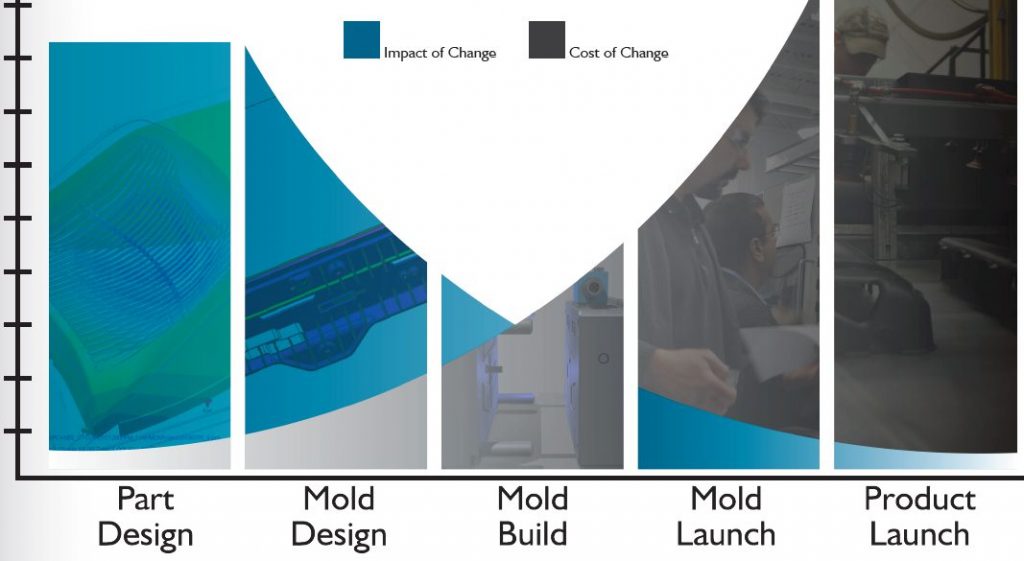
The 5 Pillars of APQP
- Plan and Define: Link customer expectations, wants, needs, and desires to requirements
- Part Design: Capture geometry, design features, details, tolerances, and refinement of special characteristics
- Process Design and Development: An extension of part design
- Validation: focus on process quality and volume capabilities. Typical tools used are Statistical Process Control (SPC), Measurement System Analysis (MSA), and Process Capability Studies
- Assessment and Corrective Action: An in-depth exploration of all ongoing manufacturing processes, focusing on reduction of the current RPN scores, and a look at if there are any internal/external corrective actions that can be done
Conclusion
In conclusion, the incentive for using APQP is the potential to achieve a successful product launch with minimized product and process risks. APQP also allows you to improve your manufacturing process, reduce variations, and improve part quality while increasing your overall customer service and satisfaction.
Download our white paper to learn more about the 5 pillars of APQP.