Innovative technology, training, and
consulting from design to production
Technology
Gain a competitive advantage through the industry’s latest injection molding process control software while improving productivity, minimizing waste, and enhancing profitability. Our full-service, custom technology solutions are built to solve the challenges you face every day.
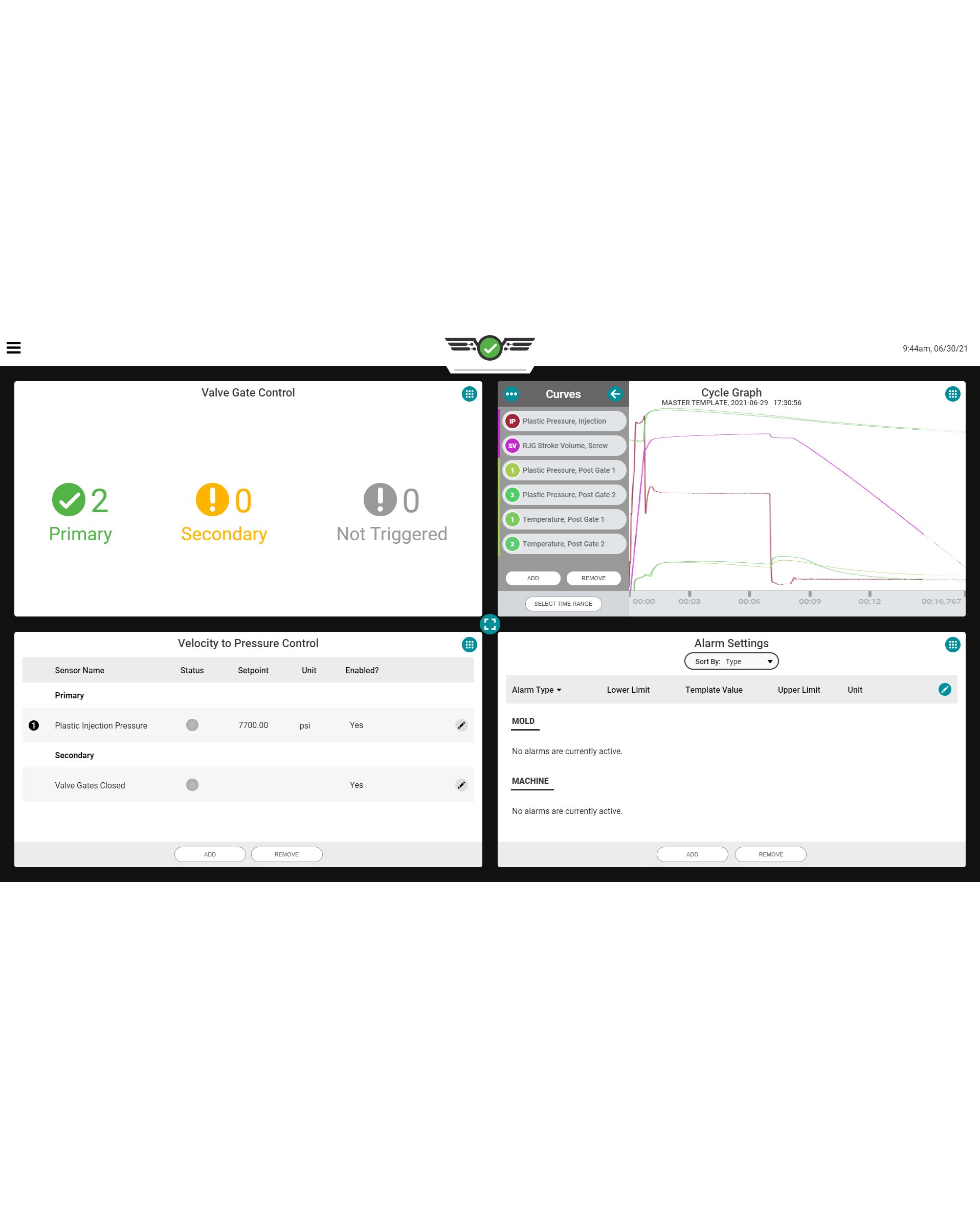
Training
Trained staff improve product quality, efficiency, morale, and turnover. Our global in-person and online injection molding training courses are led by industry experts with real-world injection molding experience and tailored to your unique needs.
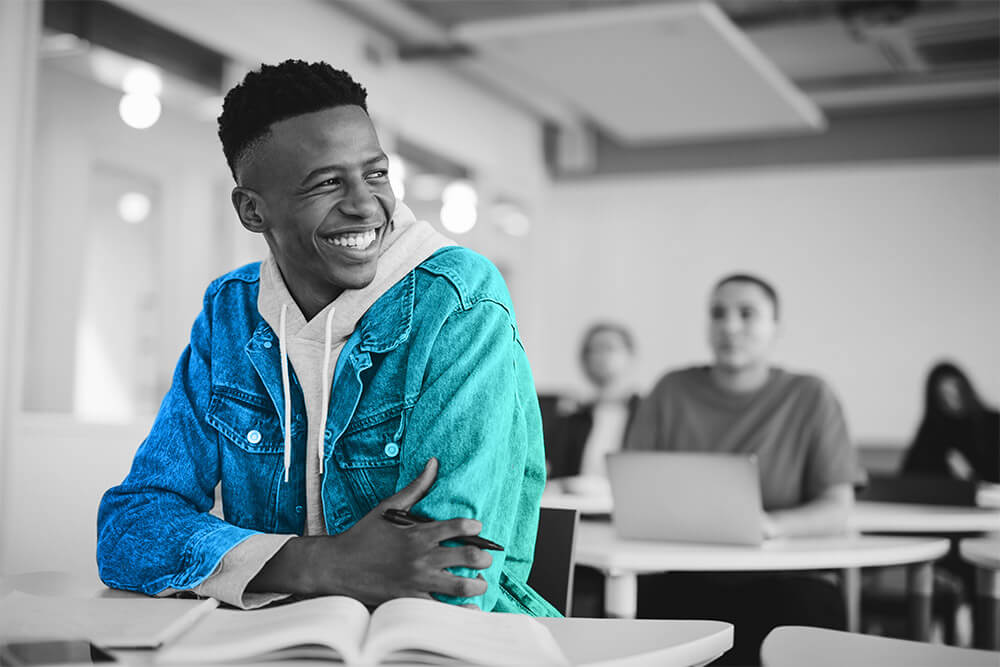
Consulting
Harness our consultants’ extensive industry experience to fix ongoing challenges in already established molding processes. Reduce waste from art to part with streamlined tool launches so you can start making good parts from the first shot.
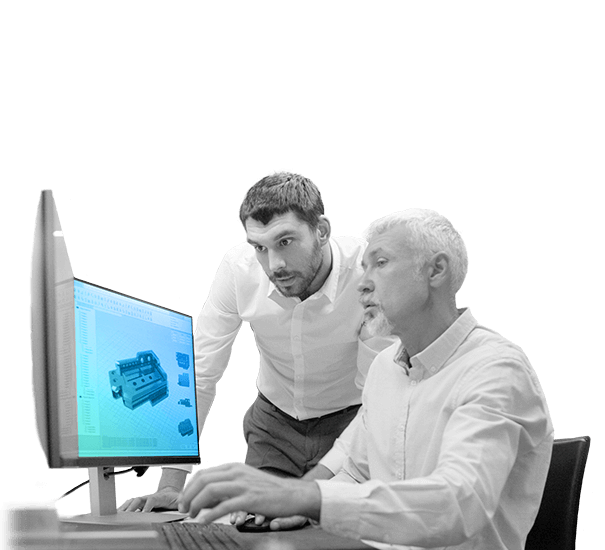