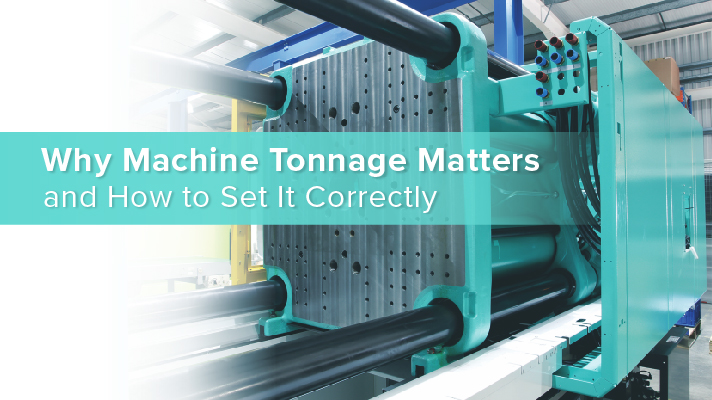
We often see injection molders running machines with inappropriate tonnage—it’s something many people either overlook or don’t believe has a big enough impact to affect the end part. But the truth is, having the wrong tonnage can lead to a lot of issues, not the least of which is shipping bad parts to your customers.
So what is tonnage, why does it matter, and how do you calculate it?
What Is Tonnage in an Injection Molding Machine?
Simply put, tonnage is the amount of force needed to keep the tool closed during the injection process. This clamping force is measured in tons and is vital to know in order to select an appropriate injection molding machine. A small machine may only be 25 tons, and they range up to 4,000 tons and beyond.
Why Does Injection Molding Tonnage Matter?
There are several issues that can occur due to inappropriate injection molding machine tonnage. Here are three of them:
1. Burn
When you clamp up a tool, the cavities fill up with air that needs to be released. To do this, toolmakers install a small channel in the parting line called a vent. These vents are not very deep, only around 0.001 to .0015 inches on average, so we need to be careful not to pinch them shut with too much tonnage. If more tonnage is applied than needed, then the air will be trapped causing a defect known as burn. This burn is caused by the compression of air at the flow front. As the air compresses, it heats up to the point where the material starts to scorch.
2. Pressure Loss
When you shut off the vents by using too much tonnage, you additionally increase the pressure it takes to fill the mold. Quite simply, any time you increase the amount of pressure it takes to fill a mold and drive plastic to the end of the cavity, you increase the variability of your process. We typically refer to this as pressure loss. You can look at pressure loss like playing darts. The higher the pressure loss, the further you step away from the dartboard. We have enough things working against us in the process—why add more to the problem? By keeping the tonnage to an appropriate level, we minimize the pressure loss in the tool.
3. Mold Damage
Another long-term problem with using too much tonnage is the wear and tear on the mold. Let’s face it, molds wear out over time, so why accelerate that by running a mold with excess tonnage? The mold tonnage will continually press on the parting line, wearing it out prematurely. We have seen molds so worn, that when the tonnage was reduced to normal level, the mold flashed.
How to Calculate Injection Molding Machine Tonnage
So we know how important appropriate tonnage is, now let’s explore how to set it correctly.
The first thing we need to do is calculate the projected area of the parts and runner as seen at the parting line. This is the area where plastic projects itself on the cavity and attempts to force the mold open.
Once the area has been calculated, we need to apply a tonnage factor. Tonnage factors are commonly called out in processing guides as 3-5 tons/in2 of projected area. We typically teach that 3 tons/in2 is a safe number to use. The tonnage factor depends on the thickness of the part. Generally speaking, a thinner walled part will need more tonnage than a thicker part.
Sample Calculation of Machine Tonnage Requirements
Please note: this calculation is considered to be a theoretical, predicted value, and we recommend performing a clamp force optimization study to determine what is actually required by the mold as it operates in the particular machine in which it is mounted.
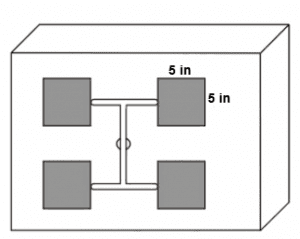
1. Calculate part area:
For this mold, the area of each part is 5 in x 5 in, so 25 in2
2. Calculate area of the runner:
The projected area of the runners in this mold is 10 in2
3. Determine the total projected area of the part:
Total projected area = (part area x number of cavities) + area of the runner
So for this part, it would be: (25 in2 x 4) + 10 in2 = 110 in2 is the total projected area
4. Find tonnage factor of that material in the spec sheet:
The tonnage factor for this material is 3 ton/in2
5. Calculate tonnage needed:
Tonnage needed = total projected area x tonnage factor
So for this mold, it would be: 110 in2 x 3 ton/in2 = 330 tons
The required injection molding machine tonnage for this mold is 330 tons.
Conclusion
Having appropriate injection molding machine tonnage is vital to ensure a good process and good parts for your customers. Applying the correct tonnage to a mold will save you from part defects, increased process variation, and wear and tear on the mold. A win, win, win by any measure.
Want to learn more? Check out our Fundamental of Systematic Injection Molding Course.