There is metal everywhere! And here I thought we were making plastic parts… Actually, there is a surprisingly significant amount of metal that is used in the manufacturing of plastic molded parts.
The Screw and Barrel
On the molding machine, one key area that must be considered is the screw and barrel assembly. It takes a significant amount of energy to melt plastic through mechanical friction, but the type of resin being melted impacts the steel selection.
For general purposes (materials like polypropylene), a standard steel will work just fine. However, not every material is as easy to work with. Materials that have glass fillers can quickly erode a soft steel selection, reeking all kinds of havoc on part quality. For aggressive materials, such as a 33% glass filled PA, it’s recommended the screw and barrel assembly be constructed of a CPM 9V or similar type steel, which has a higher wear resistance.
The Tie Bars
Tie bars are another important feature on the molding machine. Tonnage is created when these massive steel rods are stretched in tensile. All four rods must stretch equally to provide even clamping forces across the mold surface. If the difference is large enough, it can cause premature failure of the mold or even cause a tie bar to snap. Speaking from experience, neither of these situations is pleasant. In Image 1 below, there is a visual gap between the back of the platen and the tie bar nut. In this example, the machine was set to run at 50 tons. With 4 tie bars, each should provide 12.5 tons of force, however due to improper torque, the tie bars were stretching at different rates.
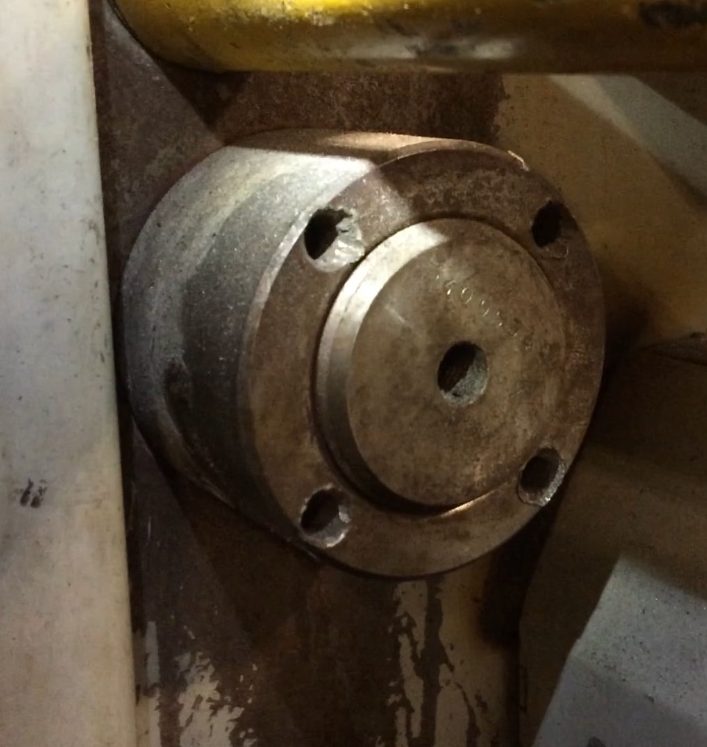
The Platen
Platen stiffness is critical to the overall longevity of both the mold and the machine. Platen must be stiff to provide a rigid structure for the mold to be pressed against during injection. This is completed with two factors: the type of metal that is selected and the shape of the support structure opposite the mold mounting surface. If the platen is not properly designed, the mold will typically flash around the sprue. This is because the highest pressure is at the sprue and the least amount of support is typically in the center of a toggle type clamping system (shown in Image 2).
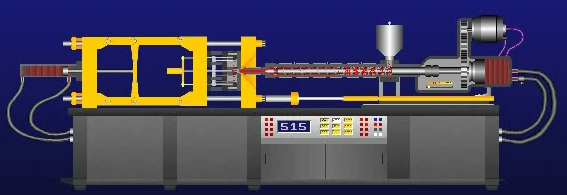
Material Considerations for Steel Selection
Understanding the material that is going to be processed also impacts the cavity and core steel selection. When processing materials that are abrasive, like the 33% glass filled nylon mentioned earlier, choosing the appropriate mold steel is critical. In this instance, selecting a steel like H13 with a high Rockwell Hardness will improve the overall durability. Conversely, if we are molding a PP resin, a P20 likely will be the correct choice for the application—they are softer and transfer heat more effectively. One item to always keep in mind is that there is a balance between hardness and thermal conductivity (Image 3).
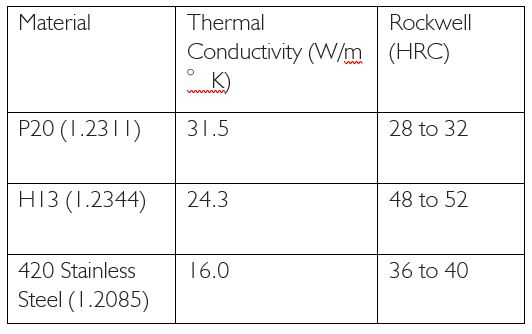
In certain circumstances, like in the medical arena, our hand might be forced into using something like stainless steel, which does not transfer heat well. For injection molders, time is money. When a steel is selected that doesn’t transfer heat well, the ability to achieve cycle times becomes increasingly difficult.
Conclusion
Metallurgy is only one of six injection molding areas you need to master to become a plastics pro. Learn all of them in our latest white paper.