
How electronics molders save money with RJG
With our custom end-to-end solutions, electronics molders are able to reduce part variability in high-cavity, thin-wall, high-tolerance, and high pressure processes. They can also easily match templates to other machines to make mold transfers quick and painless with our process control and networking systems. Training ensures staff are running as efficiently and competently as possible while speaking the same language across departments.
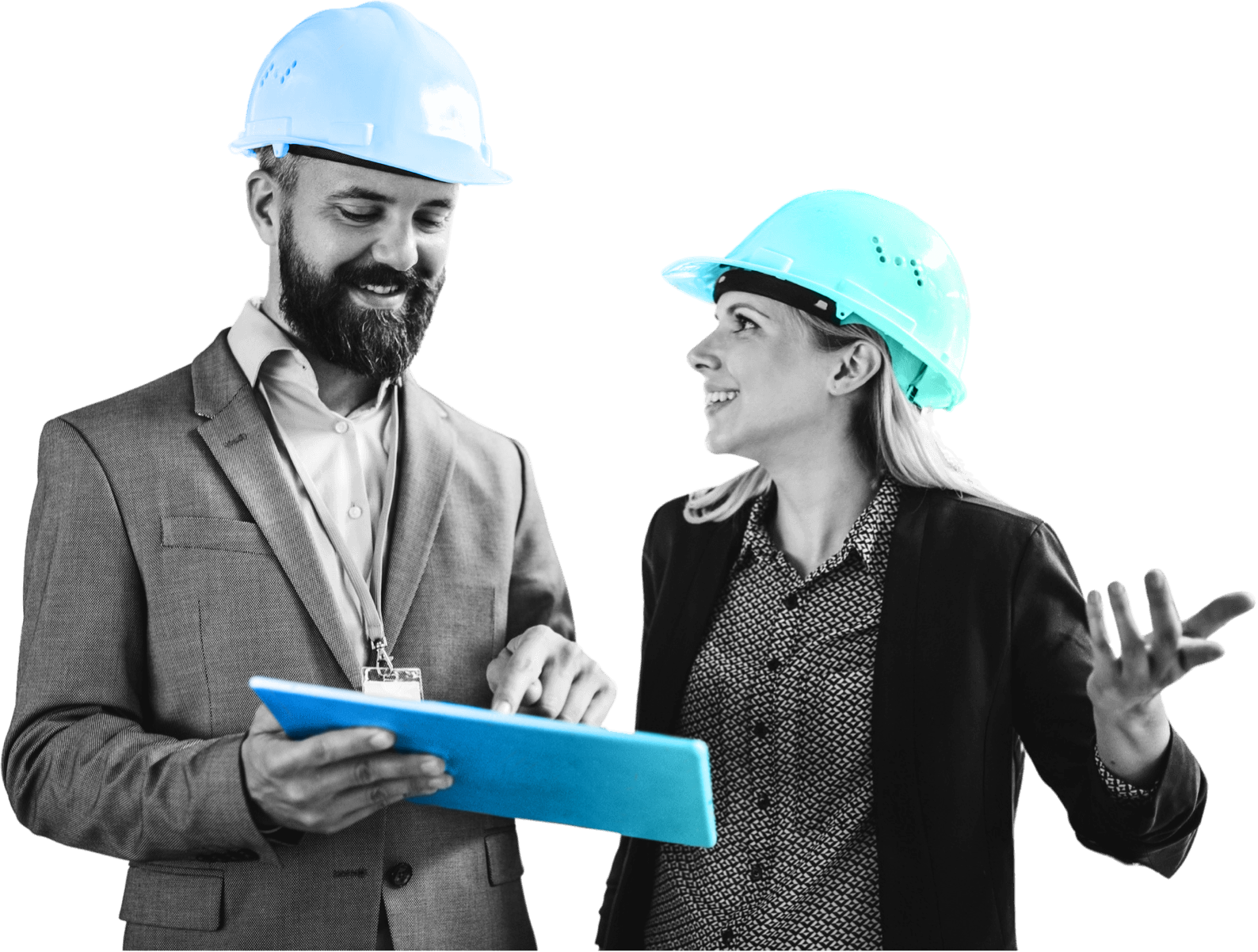
How are we different from other injection molding solutions companies?
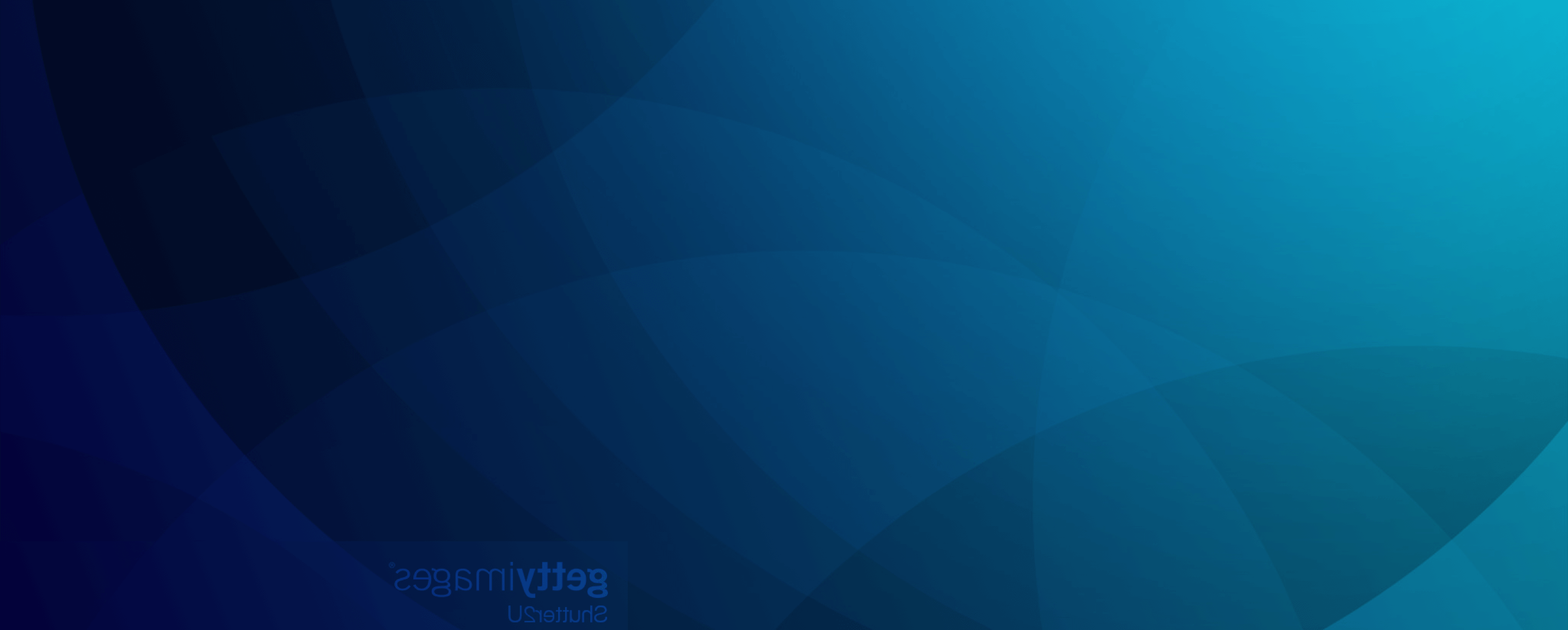