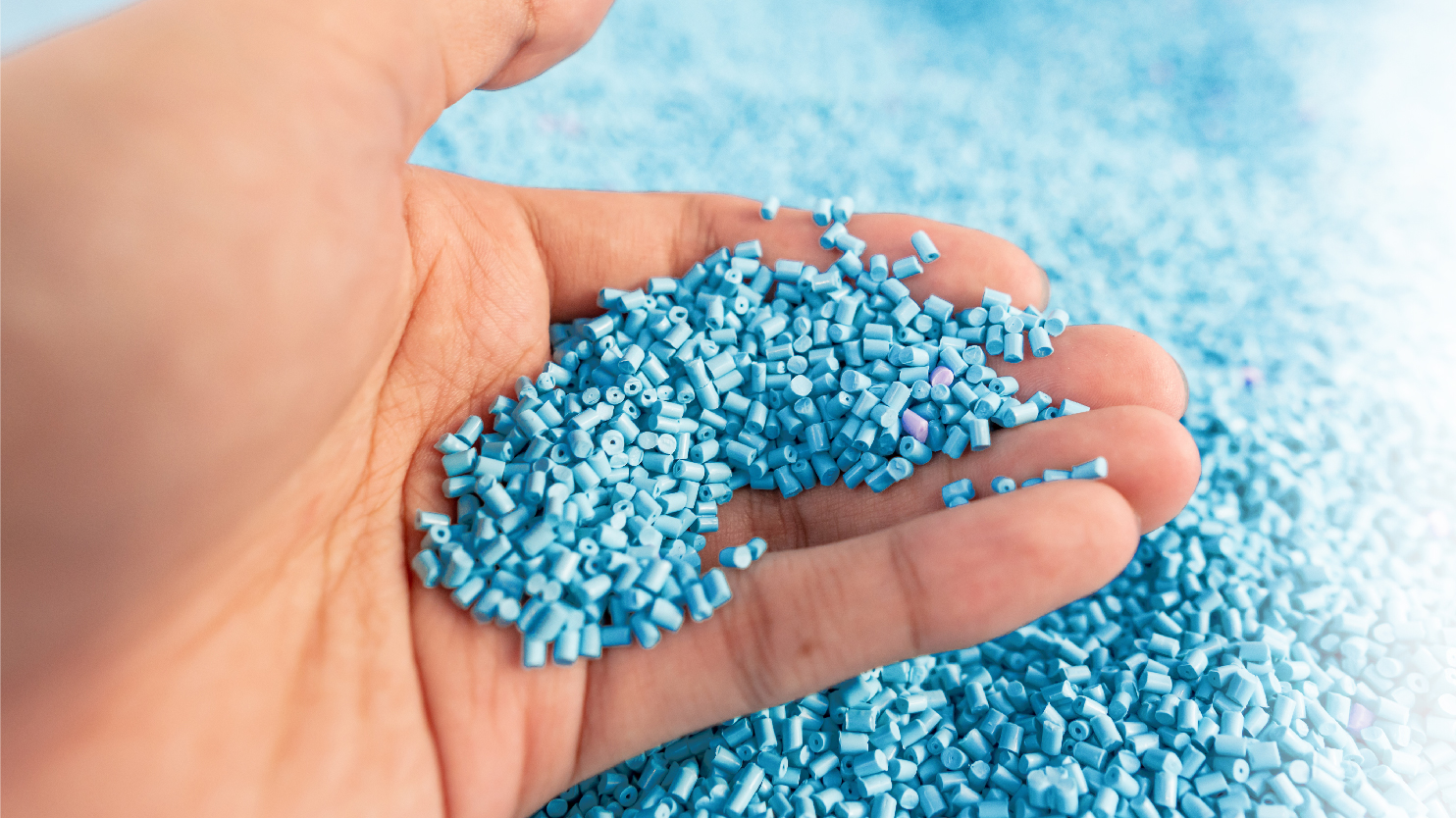
As injection molders, our natural inclination is to look at the process from the perspective of machine settings, such as barrel temperature, injection speed, or mold heater temperature. But there is a better way. Let’s review the four plastics variables and how to use them to determine what changed in your process.
What Are the Four Plastics Variables?
Making one good part is relatively easy, but making thousands or millions of good parts consistently is a bit more challenging. When things inevitably go wrong, we have to ask ourselves, “What changed?”
That’s where the four plastics variables come in. They allow you to understand what is actually affecting part quality separate from machine settings. If we look at the process independent of the machine, we should be able to replicate that process on any machine.
The four plastics variables are: temperature, flow, pressure, and cooling. These are in the order that the plastic itself undergoes. It is essential that we check the variables in this order so that we do not affect earlier parts of the process as we go.
Temperature
Our first plastic variable is perhaps the simplest to understand: temperature. When looking at temperature, the first thing we ask ourselves is: how hot is the plastic?
If it’s too hot, cool it down—too cold, heat it up. There are several machine variables that we can use to create that change, but as long as we get the temperature back to where it should be without changing the other three variables, we should be alright.
Flow
Next comes the slightly trickier flow. When looking at flow, we ask ourselves: how much plastic are we moving, and how fast are we moving it?
To determine how much we are moving, first we will remove pack and hold then weigh a short shot. This tells us how much plastic we are injecting into the mold during the flow portion of the process. If we are moving too much or too little, we can adjust the amount by changing our shot size and/or transfer position.
Our actual speed is indicated by the fill time. Much like how a police officer doesn’t care what you read on your speedometer, we don’t focus on the injection speed setting. Rather, we want to see how long it actually took to get from point A to point B. That’s the fill time.
Pressure
Once flow is over, the plastic begins to enter the packing, or pressure, part of the process. When looking at pressure, we ask ourselves: how hard are we packing and holding, and for how long?
Answering how long we are packing and holding is just a function of the pack and/or hold timer. In order to determine how hard we are actually packing, however, we need to know the intensification ratio of the machine (or the ratio between the hydraulic pressure setting on the machine and the pressure the plastic actually experiences).
Intensification ratios vary dramatically. Without knowing our particular machine’s intensification ratio, we have no idea how hard we are actually packing it out. There are other variables that may affect actual plastic pressure, like mold deflection or check ring leakage. Without an instrumented mold, we are not able to confirm with absolute certainty that the pressure in the mold is the same. Helping to verify these kinds of questions is one of the major advantages of instrumented molding.
Cooling
Lastly we come to cooling, the most often overlooked plastic variable, which is ironic since it typically makes up at least 60% of total cycle time. When looking at cooling, we ask ourselves: how fast are we cooling it, and for how long?
As with pressure, “For how long?” is relatively straightforward to answer—we just look at actual cooling, take out, and cycle times and verify that they haven’t changed.
Remember that from the plastic’s point of view, cooling continues until the entire part has reached room temperature. This may take hours for thick wall parts collected in a gaylord.
The two variables that we have at our disposal to affect cooling rate are plastic temperature and mold temperature. The greater the distance between the two of them, the faster the plastic will cool down. We’ve already verified our plastic temperature, but mold temperature will have to also be checked.
The best way of doing this is by measuring steel temperature directly from the mold or measuring part surface temperature after ejection and comparing these numbers to values that we recorded when we created the process initially. If we observe a change, it’s time to look at things like actual water temperature, mold cleanliness, condition of water lines and passages, etc.
Conclusion
If we come to the end of reviewing the four plastics variables and the process is the same as before but the parts are still different, the problem must lie somewhere else—perhaps with the mold or the material itself. At the very least, if we can answer the above questions, then we’ve been able to systematically eliminate the process itself as the source of our variation. A systematic way of finding changes is the first step to moving away from the “finger pointing” that plagues far too many shops and moving toward a focus on finding solutions.