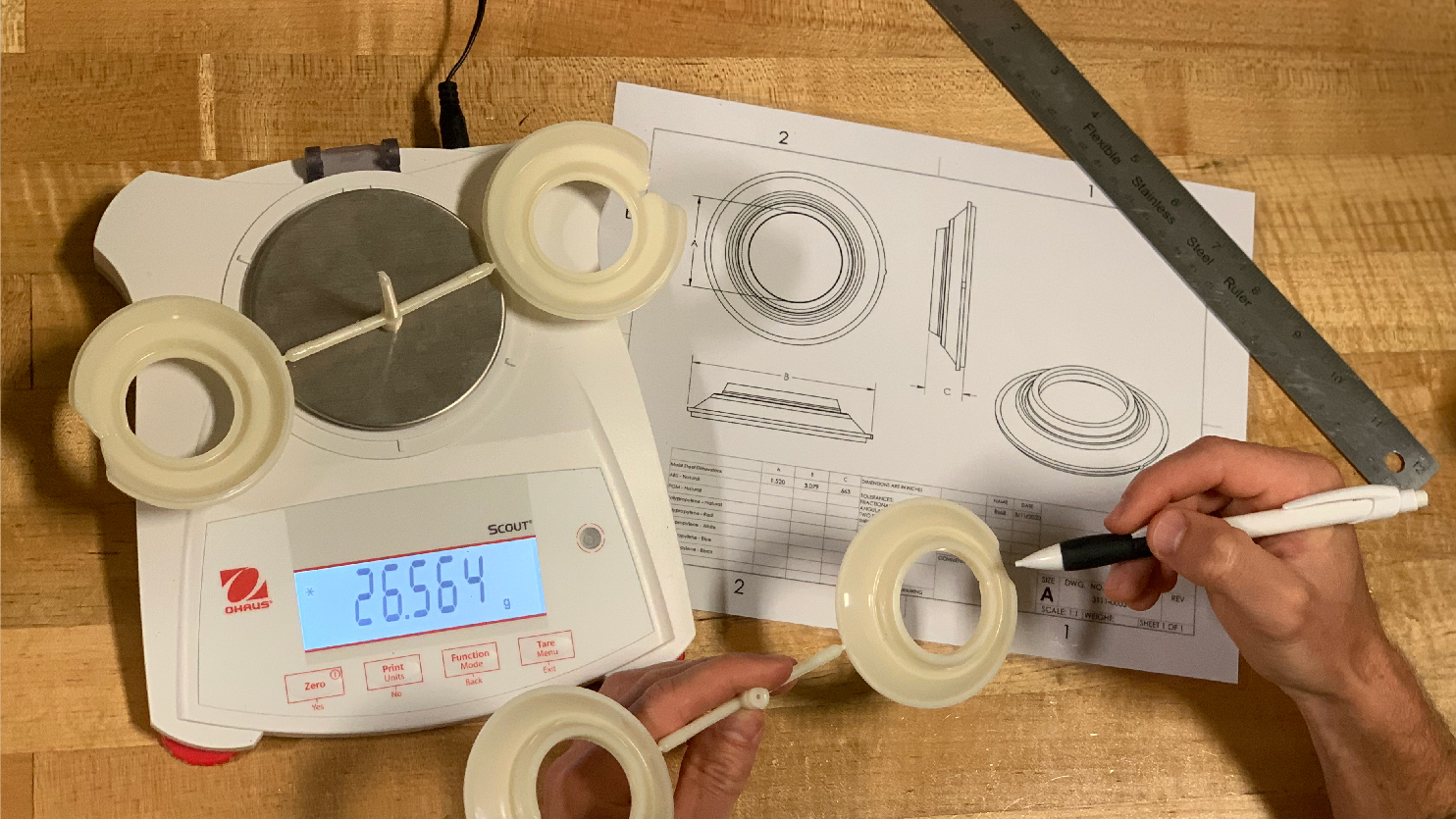
We know what you’re thinking… there are definitely more than two causes of plastic injection molding flash, but just hear us out.
First, a Story
A few years ago, we were called into a client who was dealing with a mold that he couldn’t run without flashing. He said he tried every solution possible, and he wanted us to make sure he wasn’t doing anything to cause the issue.
When we arrived to see a brand new 16-cavity mold we figured it was a processing problem, because how could a brand new mold be flashing so badly? So we started it up, and sure enough, the mold flashed across the parting line into the other cavities.
After doing everything we could within the process to fix the issue, we decided to try spraying bluing compound down the stationary side of the mold then clamping it up. Lo and behold, we only transferred about 50% of the compound—the mold was not shutting off.
So back to the toolmaker it went.
What Is Flash in Injection Molding?
Let’s start at the beginning. Injection molding flash is a common molding defect where excess plastic flows outside of the cavity, causing a flap of excess material.
The Two Causes of Flash in Injection Molding
Yes, the above was an extreme example, but it shows that you can’t rule anything out when dealing with a potential problem. Flash is quite simply caused by one of two issues:
1. Mold damage (parting line damage can’t be processed around, so please stop trying)
2. Pressure in the cavities exceeds the tonnage
There are several ways pressure in the cavities can exceed the tonnage, which are probably the causes of flash that came to your head initially: shot size is too big, transfer position is too low, hold pressure is too high, tonnage is too low, and so on.
How to Troubleshoot Flash
We always start troubleshooting flash with a fill-only part. When second stage is turned off, the part should come out 95-98% full. If it is too full, then the likelihood of flashing increases. Adjust the shot size as necessary to get the fill-only part back to where it needs to be.
Check out this video on how to establish a fill-only part.
Once the fill-only part is firmly established, we need to take a look at the second stage pressure. We would start by putting the machine settings back to the standard for the job and seeing what happens. If the parts are free of flash, then job well done.
If they aren’t free of flash, then we need to look a little deeper. Make sure that the amount of tonnage is correct. Remember when calculating tonnage, you need to make sure there is enough to accommodate for viscosity shift. It may have been correct for a while (perhaps until the material lot was changed), then viscosity dropped causing an increase in cavity pressure—hence, the flash.
Conclusion
Flash is always caused by either mold damage or too much pressure in the cavities for the tonnage. Just remember to refer back to these two causes of flash and then systematically walk through the steps to achieve a non-flashed part.
As always, we are here for support if you need us!