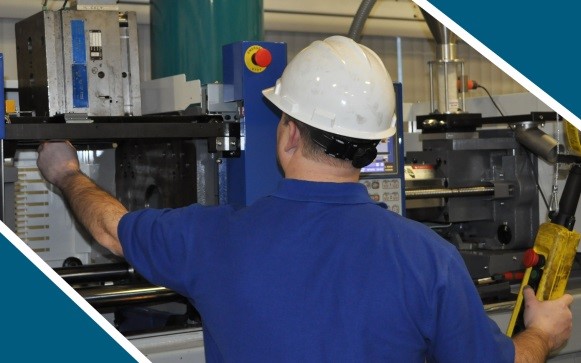
Making sure that the right mold is put into the right machine is something that could use a little more attention, for a couple of reasons.
First is the issue of machine performance. While working with many molders in the medical industry, one issue that we see time and time again is the question of barrel capacity. A common issue with high cavity, small component medical molds is too much barrel capacity. In these types of molds, medical molders are typically forced to purchase a larger machine for tie bar spacing, which can lead to a barrel that is larger than necessary. We typically recommend running shot sizes between 20 and 80—ideally 40 to 60—percent of the barrel capacity. In the circumstance of a larger barrel, however, machines often run well below the 20 percent mark. This can lead to potential problems that boil down to residence time. When running low barrel capacities, residence time on the material will typically increase, raising the risk of material degradation. With many medical molders that run polycarbonate, acrylic, and polyester materials, the degradation could show up as discoloration of the material or black specs. The saving grace for most are cycle times that are quick enough to move the material though the barrel and prevent this from happening.
Occasionally, we run into the rarer problem of being above 80 percent of the barrel capacity—the opposite issue of too much residence time. This high capacity may not allow enough residence time to adequately melt the polymer. Also, an issue we see when using most, if not all, of the barrel is that cycle time may be dictated by how fast you can plasticize. We commonly refer to this as “recovery limited”. We have seen some success with customers who retrofit machines with electric screw drives to help with the ability to recover faster. Shut off nozzles are also an option, but at the expense of increased injection pressure and pressure losses.
The second issue is the consistency in the injection velocity. Realistically, how fast can a molding machine accelerate to an injection rate of 15 inches per second in ½ inch of screw stroke? This is an unrealistic expectation put on the molding machine. The analogy that we use in our classes is to get into your car and go from zero to maximum velocity and then stop in a quarter of a mile. What would be the maximum speed achieved while still being able to stop in the given distance? Now do it 10 times and achieve the same maximum speed every time. I don’t know what kind of car everyone drives, but I know mine couldn’t do it!
Here is the good news: when this situation occurs and the machine size is being dictated by the size of the mold, the mold deflection is minimized. Most machine manufacturers suggest using 66 percent of the platen, but in these cases it is more like 99 percent. This is a good thing. The more of the platen that is being used by the mold, the more supported it will be, minimizing the potential for mold deflection.
Remember, when you find yourself in these situations and you need a new machine, the key is to get the smallest screw and barrel combination you can get that still works. Aim for that sweet spot of barrel capacity. Happy molding!