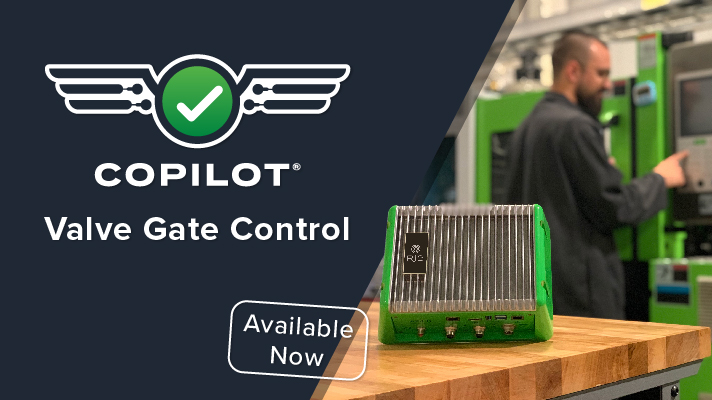
The CoPilot injection molding process control system now offers valve gate control!
Our CoPilot injection molding process control system is the industry’s latest, most user-friendly platform to produce high quality parts. It allows you to see what’s happening to the part and know the moment a process strays off template to produce less waste and more quality parts.
You can reduce risk with traceable data that proves that each shot was produced using a templated process. The CoPilot system also allows you to automatically sort suspect parts, collect data to better understand the root cause of a problem, and access data globally.
The CoPilot is now also fully equipped with the ability to perform valve gate control. You can utilize in-cavity pressure or temperature sensors to control when the valves open or close. This can dramatically reduce the effects of material changes.
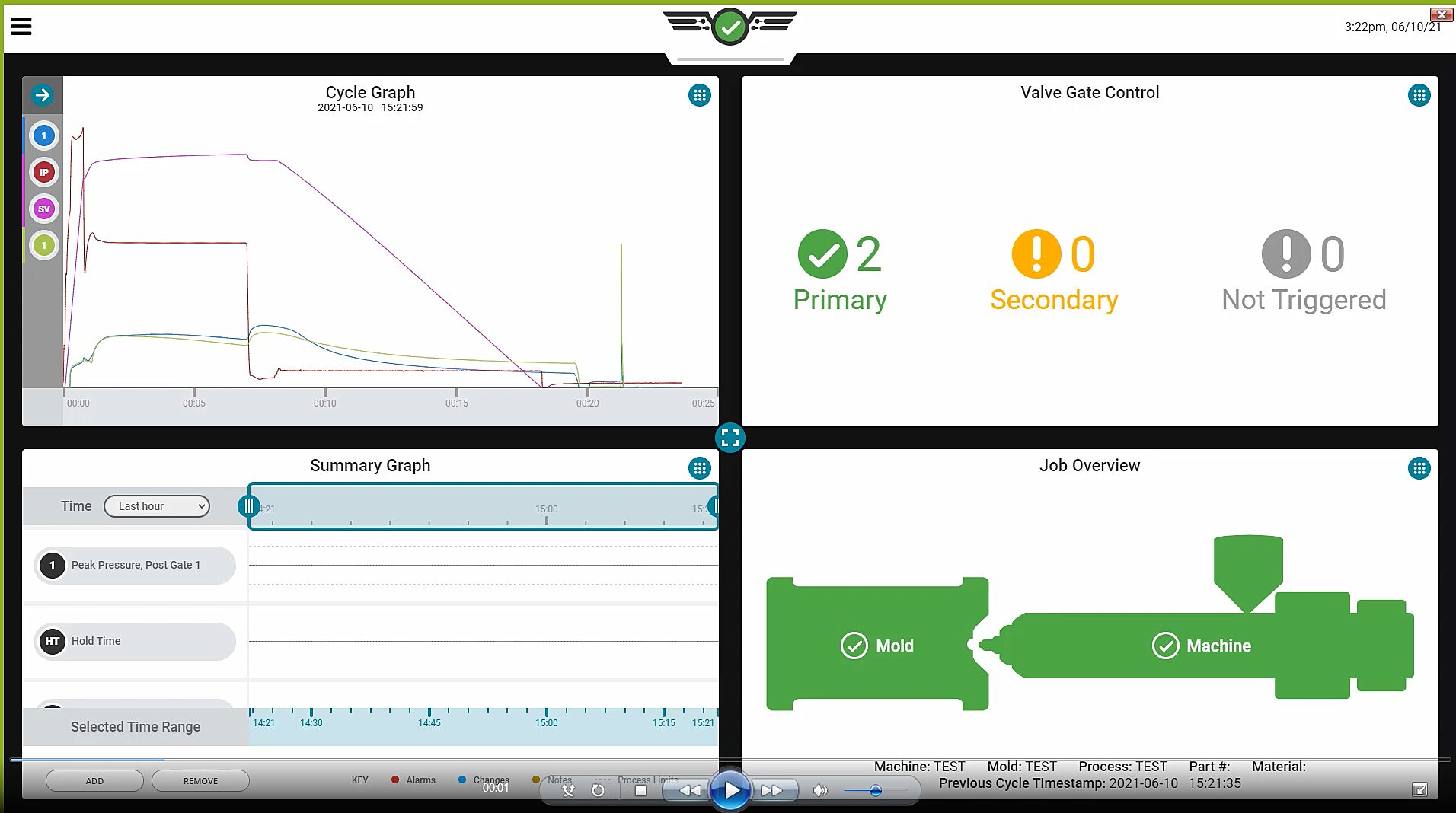
Valve gate control is ideal for:
- Large, cosmetic, complicated parts that require multiple valve gates
- Multi-cavity family tools with a gate for each cavity
- Multi-cavity tools with a gate for each cavity
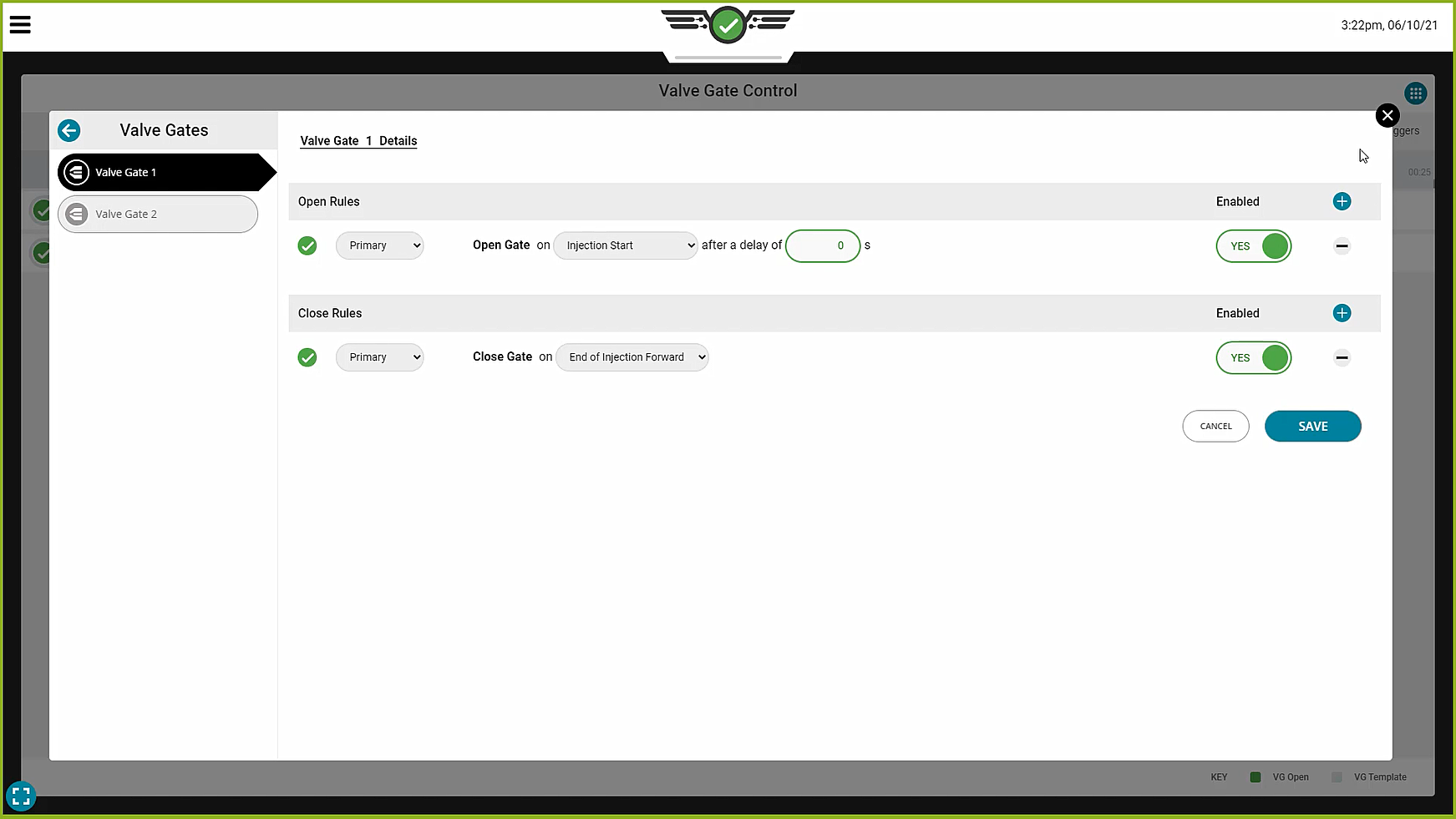
Valve gate control allows you to:
- Gain precise, individual control of flow fronts in a large multi-gate cavity
- Increase control over the removal or moving of knit lines
- Gain precise, individual control of flow fronts in cavities making different parts
- Gain precise, individual control of flow fronts in cavities making the same parts where cavity fill balance is an issue
- Improve long-term part consistency in both family and multi-cavity molds
- Maximize uptime, process capability and performance
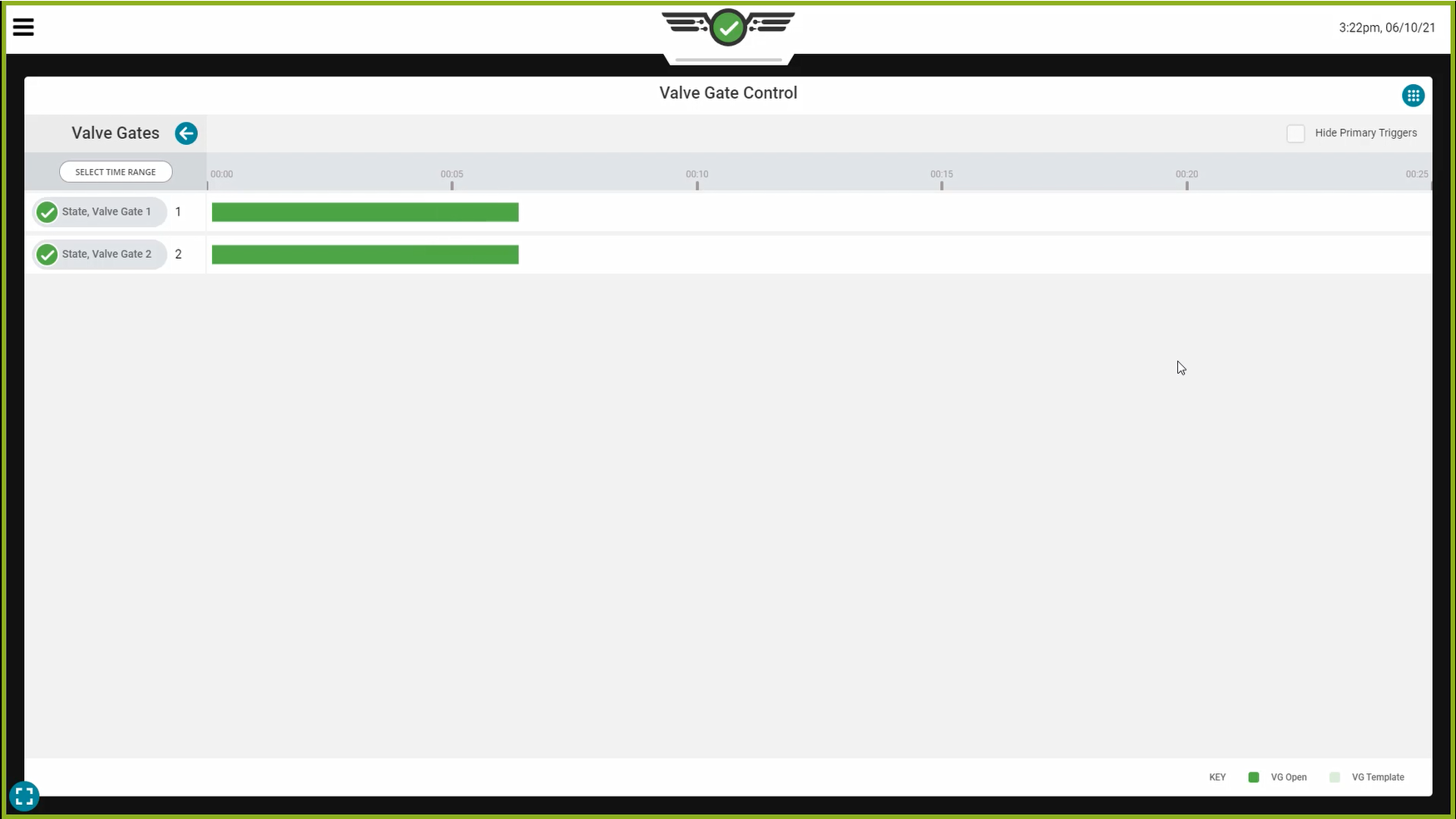
You are able to view a snapshot of how valve gates are functioning from the overview screen. By clicking into the valve gate screen, users can get more detailed information, including when each specific valve gate opened, when it closed, and if it didn’t trigger.