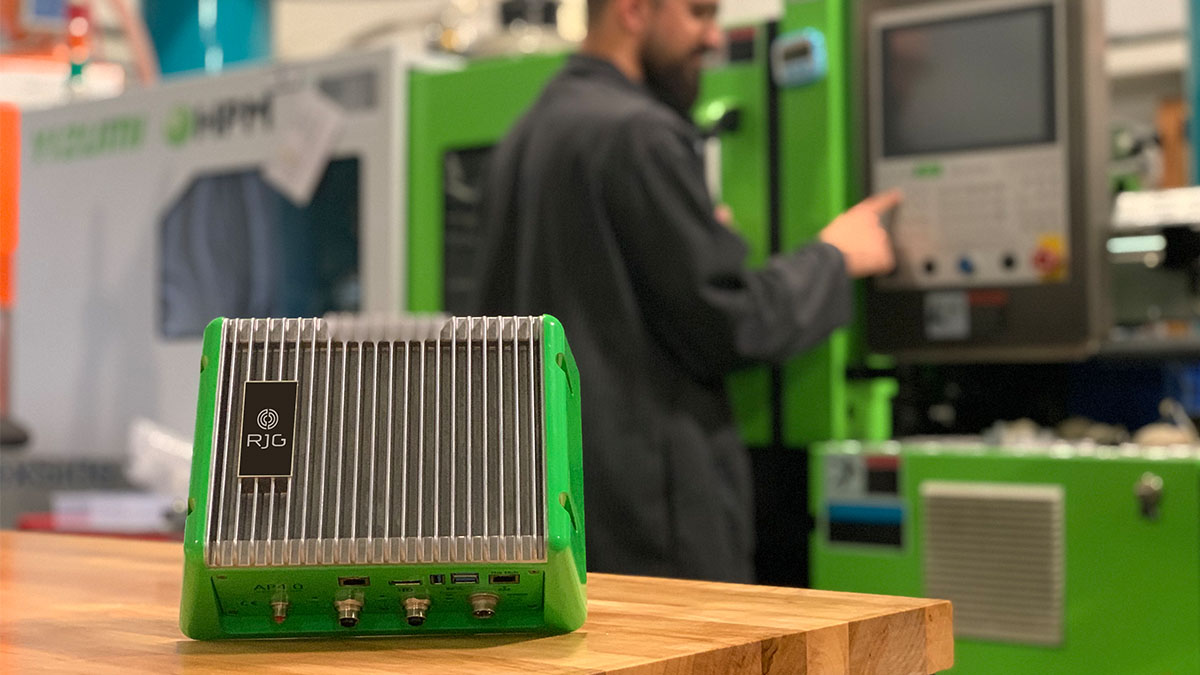
CoPilot® is the plastic injection molding industry’s latest process monitoring and control system, but it does a whole lot more than that. Here are 7 ways CoPilot can save you and your company money.
1. Save time
Time is money, right? CoPilot saves this precious resource in countless ways. Two of these ways are by automatically sorting out suspect parts and reducing machine downtime.
Automatically sort parts: Stop the time-consuming (and risky) process of hand-sorting by detecting bad parts before the mold opens and automatically sorting them out based on cavity conditions. Automation also reduces the risk of human error and greatly reduces the risk of bad parts getting in customer hands.
Reduce machine downtime: CoPilot allows you to quickly find and solve the most challenging molding problems and notifies you the moment a process strays from the template. A large, purple screen immediately lets you know that a machine is currently down, and the machine overview screen shows you where there is an issue, so you can quickly get the machine up and running again.
Sometimes all of the machines settings are to the standard, but the parts are not quite where they need to be. This is when cavity pressure template matching shows the true power of CoPilot. Through the use of cavity pressure monitoring, the cavity pressure conditions that made good parts before can quickly be achieved.
2. Reduce scrap
Scrap is wasted materials, time, and money—reducing scrap is a huge opportunity to increase your bottom line. CoPilot helps with this by preventing excessive rejects and monitoring viscosity shifts.
Prevent excessive rejects: Know the moment a machine is making reject parts with real time on-screen notifications. It’s hard to miss a large, bright red screen across the plant floor. Knowing immediately when a process has swayed off template allows you to get it back on track before too many reject parts are produced. Also, if the press produces too many rejects over a period, it can shut the press down so the issue can be addressed.
Gain control over your process: When paired with in-mold cavity pressure sensors, CoPilot allows you to gain control over your process. This opens up the possibility for DECOUPLED MOLDING® strategies to improve overall part quality and further reduce the number of suspect parts produced.
Monitor viscosity shifts: Whenever you change to a new lot number or material or introduce regrind, the viscosity can shift up or down. The CoPilot monitors effective viscosity, and alarms can be set to alert the technical staff and avoid costly time trying to identify what is causing the process to shift.
Complete dimensional correlation studies: Correlate process variables such as cavity pressure to part dimensions or hold pressure to weight. This allows you to know, with a high degree of certainty, that parts are either in spec or not.
Monitor and control water temperature: CoPilot is also compatible with Burger & Brown Flowmeters, allowing you to immediately know when water is not flowing at the correct rate or temperature, further preventing scrap and machine downtime.
3. Promote product traceability
Being able to trace all of the parts that you have produced and shipped is a huge (and very important) advantage of the CoPilot. This can be used to build audit trails to prove your parts, review past successful cycles to replicate them, see when a process changed and review what happened, and more.
Build an audit trail: Cycle data is recorded and stored, and process data from months back can be recalled and verified in a failure investigation. This allows you to see when, how, and by whom processes changed in the past and compare current cycles to past cycles. And this is all done with the click of a button—no more manual machine audits.
Reduce risk: Having access to audit trails and proof of good parts reduces risks involved should a part fail, especially a medical part. The consequences of a part failure could be dire, and reducing the risk of fallback is priceless in the long run.
Complete part sampling: Easily run quality control or group samples on the CoPilot while capturing that run in The Hub. CTQ’s can be entered and associated with a specific part, linking those parts directly to process data and providing traceability and continuity from production to quality.
4. Eliminate documentation costs
A lot of automotive and medical companies must document their process settings. Their customer and many regulatory agencies require that the settings for a validated process be recorded at certain intervals. This could be every shift, day, lot, etc.. Documenting process settings is a non-value-added activity, meaning that the company is not getting paid to have the employee go to every press and document the settings. Often the employee is taken away from a more value-added activity, like changing molds or starting up a process to go document the process, making documentation low on the priority list. Even when done, documentation is often “pencil whipped”, meaning numbers aren’t verified, just a copy of what was there before. If a non-conformance is discovered, then the documentation is now unreliable.
No more manual entries: Using the Copilot eliminates the need for documenting the process, because each cycle collects all relevant process information. These parameters are sent to The Hub® networking system and stored for a period of time. If an audit occurs requiring verification of process settings, The Hub allows you to view the process for that point in time.
If a failure investigation should arise, again the process can be viewed via The Hub and the process settings for the run can again be verified. The Copilot and The Hub system’s data collection can eliminate the need for operators and technicians to perform non-value-added activities.
5. Save and record process changes
Process changes can be documented and recalled within the CoPilot in order to see how it has changed over time, why, and by whom.
Review how the process has changed: Knowing what changed in a process is the first step in diagnosing how to resolve challenging molding problems. You can see what settings were changed and pinpoint when reject parts started being produced to fix the issue. No more wondering what happened during the midnight shift the night before.
Review who changed the process: Never wonder who made changes to your processes again—know who made changes and when so you can track the root cause of challenging injection molding issues and put the process back to how it was before.
6. Solve problems fast
The faster a problem is solved, the lower your waste, scrap, and cost and the higher your production rates and bottom line. CoPilot makes it fast and simple to get back on track and making parts you can be proud of.
Match processes to templates: Build templates that show what parameters your process should remain within in order to continue producing good parts. Once a process goes off template, CoPilot will notify you immediately so that you can get it back on track fast.
Raise production rates: By quickly solving injection molding problems and decreasing machine downtime, you can produce more good parts in less time. Higher production means a higher bottom line.
7. Improve efficiency of mold transfers
Transferring molding to different machines (especially machines with different sized barrels) doesn’t have to be complicated or costly. Through using machine independent variables and the mold transfer application on the CoPilot, you’re able to quickly and painlessly transfer molds without costly downtime and scrap.
Export machine-independent process templates: The Machine independent variables that the CoPilot uses speak the common language between different machines and gets the plastics variables correct without trial and error testing. Templates are created based upon the mold, not the machine, and can be input on the machine and CoPilot, so the process is immediately set up and ready to go.
Make good parts from the first shot: Having pre-established and proven processes allows you to make good parts from the first shot with limited need for adjustments or guess and check techniques.
Conclusion
CoPilot can save you huge in time, scrap, and cost. And (perhaps most importantly) ensure only good parts are shipped to your customers.
To learn how to best harness the power of CoPilot, take our free, online, self-paced CoPilot training course.