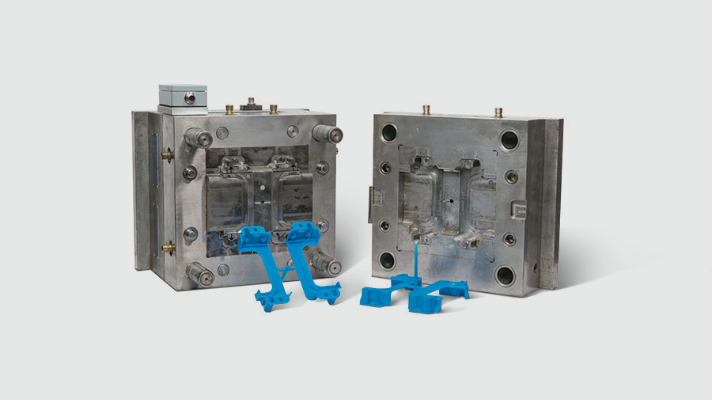
Putting a sensor anywhere in a tool can give you some form of data, but it may not be value-added. The key is knowing upfront what you want the sensor to do for you before determining where to place it and what type of sensor you want to use. Start by answering these 5 questions in chronological order.
1. What Do You Want the Sensor to Do for You?
This is the most important question to ask yourself before installing sensors in your mold. Most people stall right here because they’re not sure what functions a sensor can actually perform. A lot of people just want to instrument a tool because they’ve heard they should run DECOUPLED MOLDING® processes or they want to try out process control software. Others are curious about the ability to collect data, track a part to a molding cycle, resolve ongoing challenges, or create a template to maintain or transfer processes. Whatever the answer, this single question needs one before proceeding so you can make decisions to work toward your goal moving forward.
Once that question has been answered, we can begin to explore the many different functions sensors can serve if used correctly. Some examples are: monitoring pressure at a specific area in the cavity, transferring the injection portion of the cycle to hold via pressure, detecting mold defection, sequencing valves gates, automatically sorting bad parts, and the list goes on. Once you know what you want the sensor to achieve, you have some important decisions to make.
2. Where Do You Want to Install the Sensor?
Now to install it. Conventional installation locations to consider include Post Gate, Mid-Cavity, and End of Fill, but there are a few other locations in addition to these. You may need one or a combination of these locations depending on your particular project. In some cases, it’s not necessary to sensor every cavity.
It’s also important to note how hot the steel is where the sensors will be mounted. The electronics in the connectors of some sensor models are only rated to 140 degrees Fahrenheit, although other electronics are rated higher, and there are techniques available to mount the electronics away from the heat on hot molds.
The Benefits of Each Sensor Location
Post Gate sensors allow you to know the moment plastic enters the cavity and at what pressure. With this information, you can perform various studies, including pressure loss (from nozzle to gate), pack rate, and gate seal (pressure lost when the hold pressure is released). In addition, Post Gate sensors are often the location of choice when using Decoupled III to transfer from pack to hold using cavity pressure, but other locations can work as well depending on your machine and percentage of barrel usage.
Mid-Cavity sensors can also aid in performing calculations like determining pressure loss through the cavity and cavity deflection. In addition, they can help with timing the firing pattern of valve gates on larger parts, like car panels, where manifolds are being implemented, especially when located near each gate. Used in this application, sensors can help with moving or eliminating knit lines or reducing the flow length ratio. Mid-Cavity sensors are also a good option for very small parts, as they can typically represent an average pressure in the cavity and may be the only location available if moving ejector pins are not available at the last point to fill.
End of Fill sensors are the most common location used for automatically sorting bad parts, like short shots, using cavity pressure data. They can also monitor the pressure required to fill your part when used in conjunction with a Post Gate sensor. By subtracting the End of Cavity pressure from the Post Gate pressure, you can see the pressure loss through the cavity and observe the cooling behavior of the plastic, which is critical in semi-crystalline polymers.
Cavity Temperature sensors can be used to detect the time at which the flow front passes over a particular area in the cavity, because the temperature rises rapidly as plastic flows over them. Like Mid-Cavity sensors, this can be useful in timing the opening of sequential valve gates when the sensors are located close to each gate. Cavity temperature sensors can also measure the surface temperature of the steel, which affects part dimensions for semi-crystalline parts. They can even measure the relative melt temperature of the plastic that is passing over the sensor.
Knowing some of the different functions of instrumenting a tool will greatly aid in deciding what sensor type and location you’ll need to achieve your goal.
3. How Should You Install the Sensor?
The most common installation styles for pressure sensors are flush mount and button styles. Flush mount sensors are mounted in the cavity block so the sensing surface is in contact with the plastic. Button style sensors are mounted away from the cavity, and the pressure is transferred to the sensor via ejector pin, transfer pin, static pin, or ejector sleeve. The choice of sensor style depends on many factors, including the availability of ejector pins in the desired cavity location, the space available for the sensor, and the temperature of the mold, among others.
After decades of sensor installs, customer feedback, and testing, we strongly believe that mounting the sensor in the clamping plate and utilizing a transfer pin to transfer the pressure is the most robust configuration for most applications. Some of the benefits include:
- Mitigating the chances of damaging the sensor due to the tool’s action or while it is serviced on the bench
- Ease of accessibility
- Minimizing heat exposure to the sensor
- Improving the sensor’s life by removing it from the movement and shock of the ejector plate
4. What Type of Sensor Technology Do You Need?
The two pressure sensor technologies we offer are Strain Gage and Piezoelectric. Strain Gage sensors generally are more cost effective, require less maintenance, have more rugged cables, and are less susceptible to signal errors if water or other contaminants enter the connectors. Piezoelectric sensors are generally used in flush mount applications and in certain applications where ultra-miniature sensors are required.
5. What Load Capacity Do You Need?
For button style sensors, we need to determine the load capacity of the sensor used. The load capacity is determined by the predicted force that will be exerted on the sensor. To do this, you need two pieces of information: the projected area of the sensing pin; and the expected pressure you expect to see in the sensing location. Multiplying pressure times the area gives you the expected force. The sensor you choose must have a load capacity higher than the expected force but not so high that the sensor signal gets “lost down in the mud.”
There are several ways to determine the expected pressure. The preferred method is to use flow simulation with predictions of the pressure in your chosen area. If this is not available, you can resort to the material datasheet, which often gives a pressure or tonnage factor. This gives you the recommended pressure per square inch required within the cavity to mold that particular resin properly.
If the tool under consideration for sensoring is already built and simulations are not a luxury you have, you can perform a Short Shot Study to determine the pressure required during filling. To do this, you fill the part gradually at your preferred linear speed or volumetric flow rate and observe the filling pattern. Determining Post Gate is fairly straight forward, however determining Mid-Cavity and End of Fill can be a little trickier depending on the material, flow rate, and geometry. The key is to not make too many assumptions without supporting your decisions with actual data.