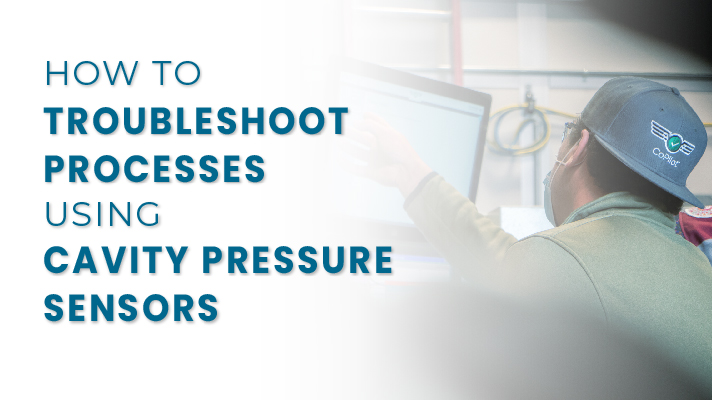
Troubleshooting is a normal part of injection molding processes, but it means something a bit different to everyone. When something goes wrong with a process, molders often look for solutions through turning knobs and pushing buttons, hoping with fingers crossed that the next parts out of the mold will be better than the last.
Sound familiar?
This method only results in wasted production time and escalated material costs. Plus, it doesn’t address the root cause, stacking up even more problems. Cavity pressure sensors allow you to better determine the real problem and address it scientifically.
The First Step
The first step in troubleshooting an injection molding process is to determine what changed. The ability to do this relies heavily on the quality of data available—if accurate, relevant data is available for the original or target process, finding a solution can be simple. The key is having that crucial information, so that when shots are fired, the trouble is killed, not just wounded.
Templates
You are able to utilize data from cavity pressure sensors to create electronic templates (or blueprints) of a process. This template represents the desired cycle based on data captured inside the mold cavity and is a visual way for you to quickly and easily see what has changed in your process. You can see how the changes you make to your process impact each cycle, removing the need to button-push.
Defects such as dimensions, flash, shorts, and part weight are directly correlated to the total volume of plastic delivered to the mold cavity, which is directly correlated to the amount of pressure in the cavity. If the cavity pressure curve reaches a peak that is lower than the template, there was less plastic delivered. If the peak cavity pressure climbs higher than the template peak, this indicates more plastic being packed into the cavity.
Containment
You can also use cavity pressure technology to immediately contain any suspect parts based on in-cavity conditions. That means no more hand-sorting and no more shipping bad parts. This is HUGE and can drastically cut down on costs, scrap, and time. Not to mention the priceless benefits of satisfied customers.
Data Trends Over Time
Troublekilling dimensional inconsistencies may require recording data over time and correlating trends in cavity pressure data to specific cycles or parts. Specific production runs, or even single cycles, can be retrieved by recalling the date and time of the cycles to be analyzed. This ability to go back in time and analyze cavity pressure information is crucial since some molding defects may not come to light immediately. Historical data also lowers liability by having the ability to track and prove every shot produced.
Gate Seal
If there is a cavity pressure sensor located near the gate area inside the cavity, it can be utilized to determine if the gate is sealed. If the gate is not sealed at the time that the holding pressure is released, plastic will discharge from the cavity back into the runner. The gate end cavity pressure curve will suddenly drop concurrent with the end of holding time. This leads to part defects and scrap.
Thermal Variations
Thermal variations, such as heater band cycles or hot runner heater cycles, often appear on cavity pressure data. This type of variation may be subtle and require more data to detect. Thermal cycles will typically be repeating cycles within the data. For example, as the hot runner heaters cycle on and off, the viscosity of the material is affected. Hotter plastic will have somewhat less resistance to flow and therefore render a higher peak cavity pressure. So the peak cavity pressure will trend up and back down with repeatable frequency from thermal cycling.
Conclusion
The benefits of having cavity pressure data are pretty clear. Data from inside the cavity is the only way to see what’s happening to the part and ensure consistent quality over time without painful button-pushing. By being able to visualize what’s happening, any changes to the ideal conditions in the mold are illuminated and can be properly addressed quickly.
Learn more about cavity pressure technology.