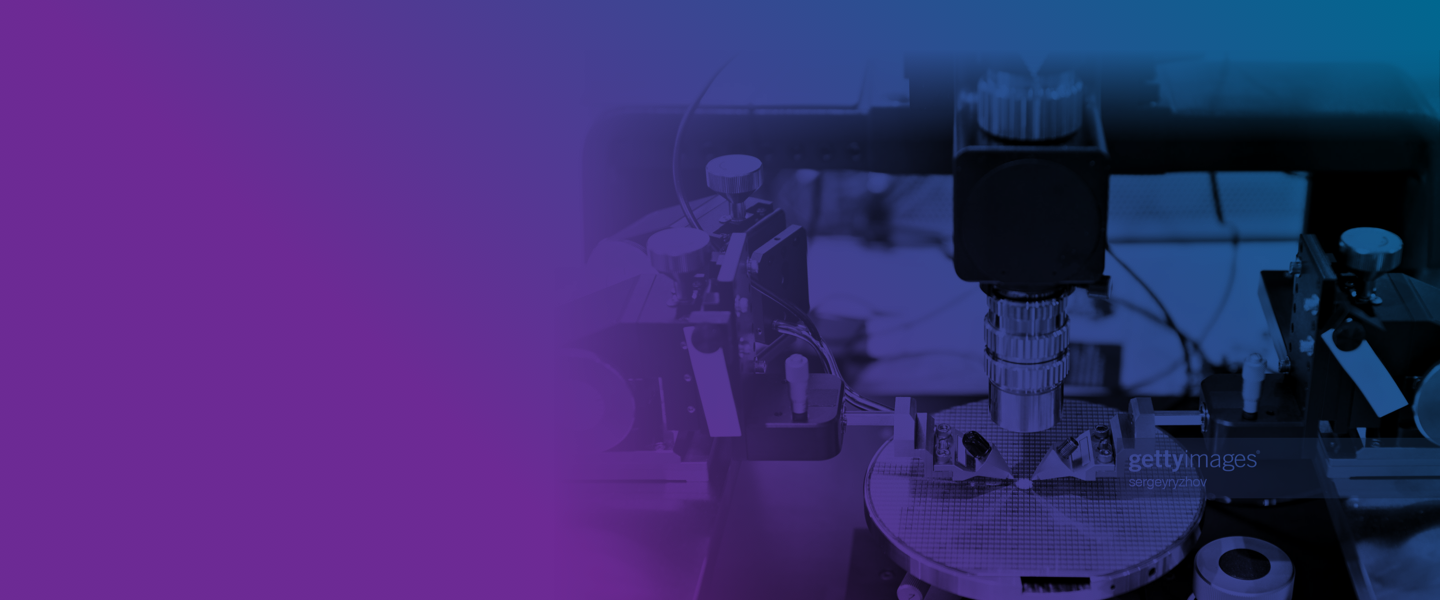
Revalidation Using Machine Independent Data
Submitted by: Rod Groleau, Chairman & CEO
As the injection molding industry continues to evolve in the face of issues such as globalization, downsizing and short run quotas, customer demands are increasing for both the mold builder and molder. More and more companies are going off shore for the production of molded components and assemblies. Mold builders and molders alike are looking for ways to streamline their processes and decrease turn around time in order to meet the demands of their customers.
Molders are facing increased demands for shorter lead times and more stringent quality requirements from their customers. For the sake of survival, they need to find progressive mold builders that have invested in technologies and strategies to help them meet today’s challenges. They are looking for ways to reduce or eliminate costly start-up runs that are time consuming and eat into the profits of the job. Optimally they are looking for mold builders that can supply Ready-To-Go-Molds that have already been put through rigorous paces and arrive at the molders door complete with a template that the molder can easily match on the production floor. What is a Ready-To-Go mold? It starts with a good mold design, which is cut properly, assembled properly, with balanced cavities, and checks must be made to ensure that all items function as designed, clearances are proper and water lines are correct based on flow. Last but not least the mold must be challenged with a rigorous mold tryout, leaving no stone unturned. The mold builder must validate mold performance requirements prior to delivery of the mold. Today, molds need to arrive at the molders door with a guarantee that the first part produced will be good, not 2, 3 or 10 shots down the line.
Molders can no longer afford to spend the better part of a day setting up a job and developing a process. They are looking for ways to streamline the initial process set-up, as well as the time it takes to repeat the set-up process when a mold is moved to another machine. In addition, many molders are required to provide data or proof that the parts they are supplying are of the highest quality. If a molding job is transferred to a new machine they are being asked to provide documentation proving that the process has not been compromised by the move. Anyone that runs a molding facility knows that moving molds from one machine to another or one facility to another as scheduling allows, is inevitable. The ability to quickly move molds from one machine to another or from one facility to another, without an abundance of downtime, is an invaluable advantage.
In summary, to remain a key competitor, companies must adapt to the new demands of the market and restructure their way of doing business to become more efficient at what they do. The best way to accomplish this may be for them to walk a mile in their customer’s shoes. Remember that technology never comes looking for you, but it sure can pass you by.