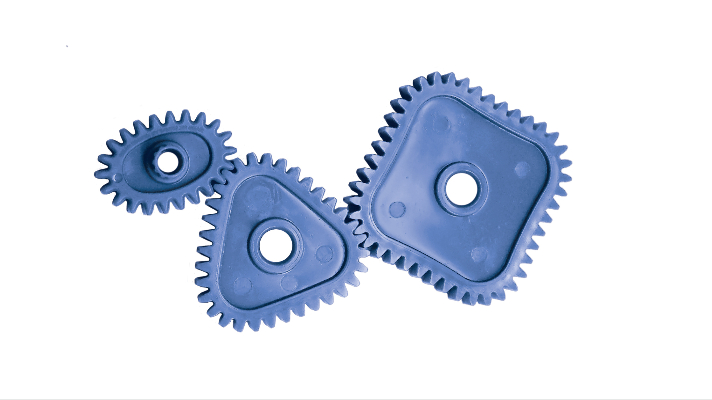
The Challenge
With all the variables in a molding process, producing a bad part is inevitable. But if you have controls in place to identify and segregate suspect parts, you can ensure those parts never reach the customer.
Six years ago, Winzeler Gear instrumented a tool with cavity pressure sensors for an automotive customer. We worked with our machine supplier to customize their controller so that we could read up to eight cavity pressure curves with the capability of making accept/reject decisions based on peak cavity pressure value. A robot was used to segregate any gears that did not meet the cavity pressure criteria. While this approach worked up to a point, we wanted to add a more scientific approach and record process data. We wanted to have a positive way of providing our customer the same parts in prototype and production and we felt that this was not only a data analysis need but also a systematic molding technique that we could teach to the entire processing group. When top management attended RJG’s Executive Overview course, we agreed that cavity pressure sensors and the eDART System™ could provide us with the data we had been looking for.
The Solution
Winzeler installed its first eDART System on one of their existing automotive applications. We did a lot of in-plant training on DECOUPLED MOLDING® and the eDART System, and continued to add more eDARTs as we became more proficient. Our goal was to launch this approach starting at the management level and push it down through the organization. We have two Master Molders and plan to have our entire upper-level molding staff certified.
The Result
Today Winzeler has 15 eDART Systems and we use cavity pressure control in every tool we build. The plant runs high-shrinkage resins such as acetal and nylon, yet still holds tolerances of plus or minus a few thousandths. We are able to much more rapidly bring production tooling on line with the help of templates created from our prototype processes. We’re taking single-cavity prototype tools, developing a DECOUPLED MOLDING process, using eDARTs to produce a molding template including cavity pressure, and then moving this straight to production. That’s how we ensure our customers get the same product in production that we gave them in prototype.
Winzeler uses cavity pressure sensing to monitor every shot. All process data is saved on the eDART System Server via wireless technology. To tie this technology together, we integrated failsafe sorting using the signal from the eDART in conjunction with the machine signal to determine if a gear is good or bad, and then segregate parts with either a robot or a diverter chute.
Cost is what keeps people from diving into this technology, but you either pay for it now or later. The bottom line is that our customers never receive process related rejects, and the overall quality rating for their end product is higher. You can’t catch everything with manual inspection, and one defective gear is too many in our customers’ eyes.
Harry Soling
Director of Manufacturing
Winzeler Gear
About Winzeler Gear
Winzeler Gear is known internationally as one of the premier designers and manufacturers of precision molded plastic gears. Over the years Winzeler Gear has expanded our manufacturing business with the assistance of our strategic suppliers and customers to create a highly automated gear molding facility with the capacity to produce 150 million gears annually. We are driven to continuous improvement and fostering innovation to continue to be a leader in the design and manufacturing of precision molded gears and actuators.