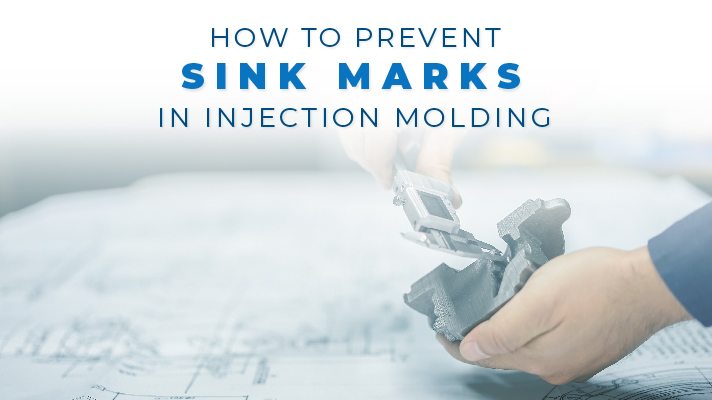
Sinks are common injection molding defects that occur in thicker sections of molded parts. Since thicker sections contain more plastic, they will naturally take longer to cool. The outer portion of the part that is in contact with the mold steel cools much faster than the internal part. As the molecules in thicker sections begin to contract, they pull in on themselves, leaving a defect known as a sink. The good news is, there are several ways to prevent them.
Here are 5 ways you can prevent sinks from happening in your injection molded parts.
1. Check Your Melt Temperature
In processing, one of the first things we want to verify to correct sinks is melt temperature. The melt temperature should be within the resin manufacturer’s recommended range. If it is too high it will take longer to cool the parts, leading to sink marks.
2. Make Sure You Have Enough Pack and Hold Pressure
If material temperature is not the cause of the sinks, we then begin to look at pressures, specifically pack and hold pressures. Pack and hold pressure (or second stage pressure) is used to compensate for shrinkage inside the mold. Thick sections of the mold will need more plastic in order to retain their shape. If there is not enough plastic in that thicker section when the molecules cool, a sink is generated.
Increasing the pack and hold pressure may increase the amount of plastic at the sink. If we can get enough plastic into the area with enough pressure, the molecules will no longer pull in on themselves, eliminating the sink.
3. Adjust Pack and Hold Time
Another processing problem that can cause a sink mark is when the pack and hold time (or second stage time) is too low. We may have the right amount of pressure, but not the appropriate amount of time. In most cases, we want to ensure our pack and hold time is long enough to seal the gate of the part, meaning plastic at the gate is solidified so no plastic can enter or exit the cavity.
Think of people in a room. If the room is crowded and the door is left open, people will naturally exit the room. Plastic is no different. If we do not wait until the gate is solidified, plastic will exit the cavity. Once plastic leaves the cavity, we can no longer compensate for the shrinkage that will occur during cooling. Increasing the hold time and verifying the gate is sealed can help prevent sink marks.
4. Avoid Excess Mold Temperature
Excess mold temperature can also lead to sinks. If the temperature of the mold is set too high, it can affect the time it takes for the gate to seal. You can find the recommended mold temperature from the resin manufacturers. Once the appropriate temperature range is established, verify that the mold is plumbed correctly and that no water flow issues are occurring.
5. Ensure Proper Part and Mold Design
Sinks can also occur due to part and mold design. Because sinks often occur in thicker sections of a part, the best approach in part design is to create nominal wall thickness, but this is not always possible. If the part is in the design phase, the thickness can be reduced by coring out those sections or by creating multiple thinner sections.
Corners can be problem areas too, since the joining of two walls can lead to increased thickness. Rounding outer and inner corners can help maintain constant wall thickness and eliminate sink.
One of the critical aspects of mold design in relation to sinks is water line placement. The thicker sections usually get adequate cooling at the part surface, however the inner portions of the thick area are often neglected. Getting water to inner portions of the thick section may be challenging but can improve sinks, part quality, and possibly cycle time.
Remember, the goal is to provide uniform cooling to the area of the part where the sink occurs.
Conclusion
There are a lot of ways to prevent sink marks from occurring in injection molded parts, and understanding how and why they happen is the first step. If you’d like help eliminating sink marks from your parts, our experienced consultants would be happy to assist.