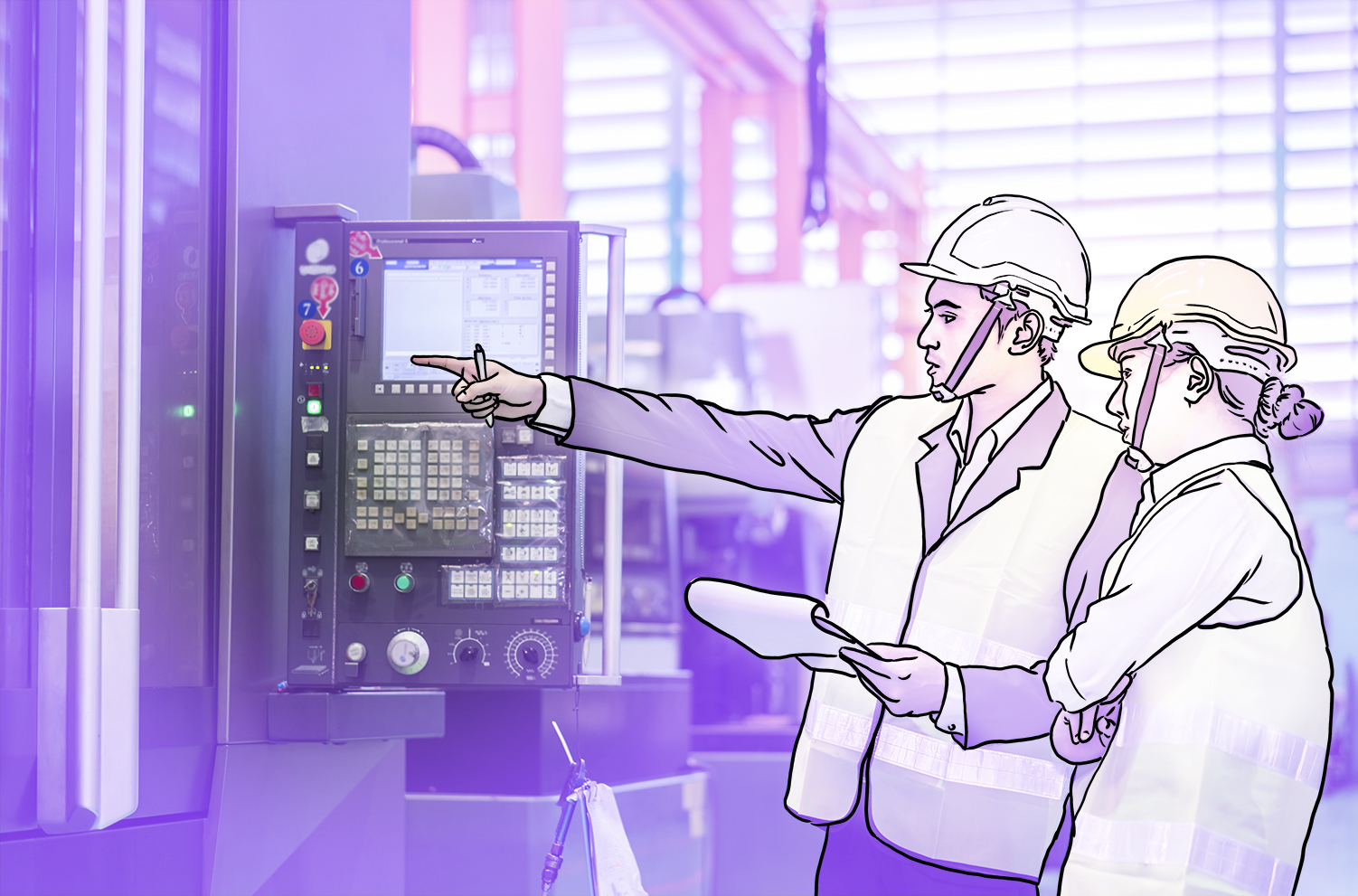
Back Pressure (BP) is always used but not always understood. Sometimes, it is no more than a value copied from a setup sheet or pulled from thin air. Then it is entered into the press only to be ignored until a defect presents itself and no other process setting solves our problem—a band aid to fix all of our problems. Here’s a quick overview of what it is, why it’s important, and how to set it.
What is BP & Why is It Important?
One of the most important requirements in injection molding is shot to shot repeatability, and melt preparation is the foundation of process consistency. So let’s focus on BP in the melt prep part of our molding process.
BP is resistance applied to the back of the screw during plasticizing (screw recovery). It tries to resist the screw achieving the shot size position. How this is done depends on the machine type.
A hydraulic machine restricts the oil flow as the cylinder, whereas a servo electric provides a breaking action on the back of the screw as it rotates. This slight resistance compresses the plastic in front of the non-return valve and makes the density of the shot consistent. This also makes the screw rotate a consistent number of times as it recovers and helps with color mixing.
Suggested BP Settings
Material suppliers and RJG recommend BP to be set to approximately 500-1,000 specific psi. This refers to the pressure in the barrel and is achieved by different hydraulic setpoints depending on the intensification ratio (see our YouTube video on the differences between hydraulic, specific, and cavity pressure).
In most applications, the optimal BP is not too far from the 500 – 1,000 psi specific range to provide consistency. It is important to understand that its purpose is for consistency, and we should use it for only that.
All too often we quickly “fix “ defects by adjusting BP. This seldom goes to the root cause of the issue. When we raise BP to make splay go away or fix a short shot, we are really increasing the density of the shot, which injects more material in the mold with the same shot size. This can be a quick workaround but only clouds the root cause. Usually, a change in BP compounds itself so that other settings have to be adjusted to accommodate for the difference in the melt density of the resin being injected into the mold. Changing the BP affects your material preparation and can throw off the fill, pack, and hold portions.
Conclusion
BP is a vital part of the injection molding process. The key is to keep things simple, leave the BP alone, resist the quick adjustment, and focus on the root cause.