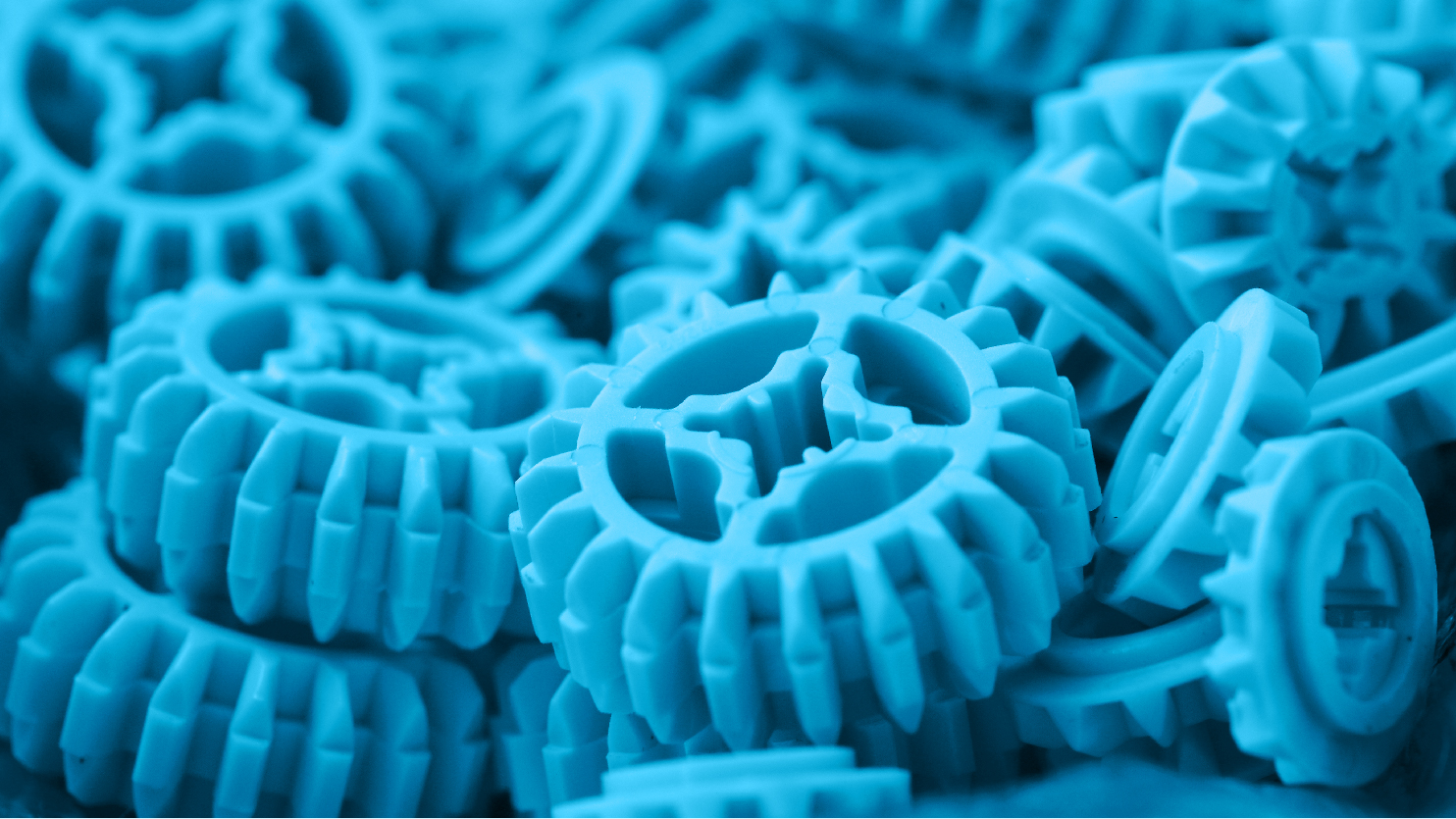
Ok, that title might be slightly misleading, because knit lines are essentially impossible to get rid of altogether. BUT there is a way to minimize them and ensure they don’t result in cosmetic eyesores or weak parts.
What Causes Knit Lines in Injection Molding?
Knit lines are formed in injection molding when two flow fronts meet in the middle of a part (a line where two sides of the plastic are “knit” together). This most often occurs when you have a core or shutoff feature that the plastic needs to flow around. Imagine a river splitting to go around a rock, then meeting up again on the other side. There’s a ripple effect, right? Same thing with plastic. But the ripple leaves a permanent line in the part where the molecules are unable to fully reintegrate.
How Can You Prevent Knit Lines in Injection Molding?
Ok, you can’t actually prevent them, but you can minimize them to make your part stronger and more attractive.
Simulation can be used to help you determine the appropriate gate location so that the knit line meets in an area that will have a lower impact on the overall fit and function of the part.
Adjust the process. Adjusting mold temperature, fill speed, and a few other settings is an easy first step to take toward improvement and could make a difference in the visual appearance of knit lines.
Switch up your materials. Different materials lead to stronger (or weaker) knit lines. For example, Thermoplastic Olefin (TPO) parts are much easier to break at a knit line than Polypropylene (PP) parts from the same mold. Even though PP is typically a weaker material, TPO is less successful at reintegrating.
Review the fillers in your material. Fiber fillers (glass) reduce strength at a knit or meld line. This is because the fibers do not melt at the same temperatures as thermoplastics, so they can’t join back together. If fiber fillers are required, short fibers or glass beads can help with strength, because they are more capable of bonding back together than long fibers.
Use valve gate control. When using multiple valve gates, controlling when they each open and close can greatly improve the appearance of knit lines. The use of cavity pressure sensors and a valve gate controller (such as the CoPilot®) can help you achieve this.
Conclusion
Knit lines are like the two sides of plastic butting heads and sticking together. There is a better, stronger connection, though. If designed correctly, a flow line has the ability to flow together and re-merge the flow fronts to become a single, stronger meld line. This is much more ideal than a knit line, as it is visually less appalling and results in a stronger, higher quality part. Check out our blog post on the difference between knit, meld, and weld lines.
So even though there is no way to fully prevent knit lines, using these techniques can help you minimize their appearance and improve overall part quality and strength.