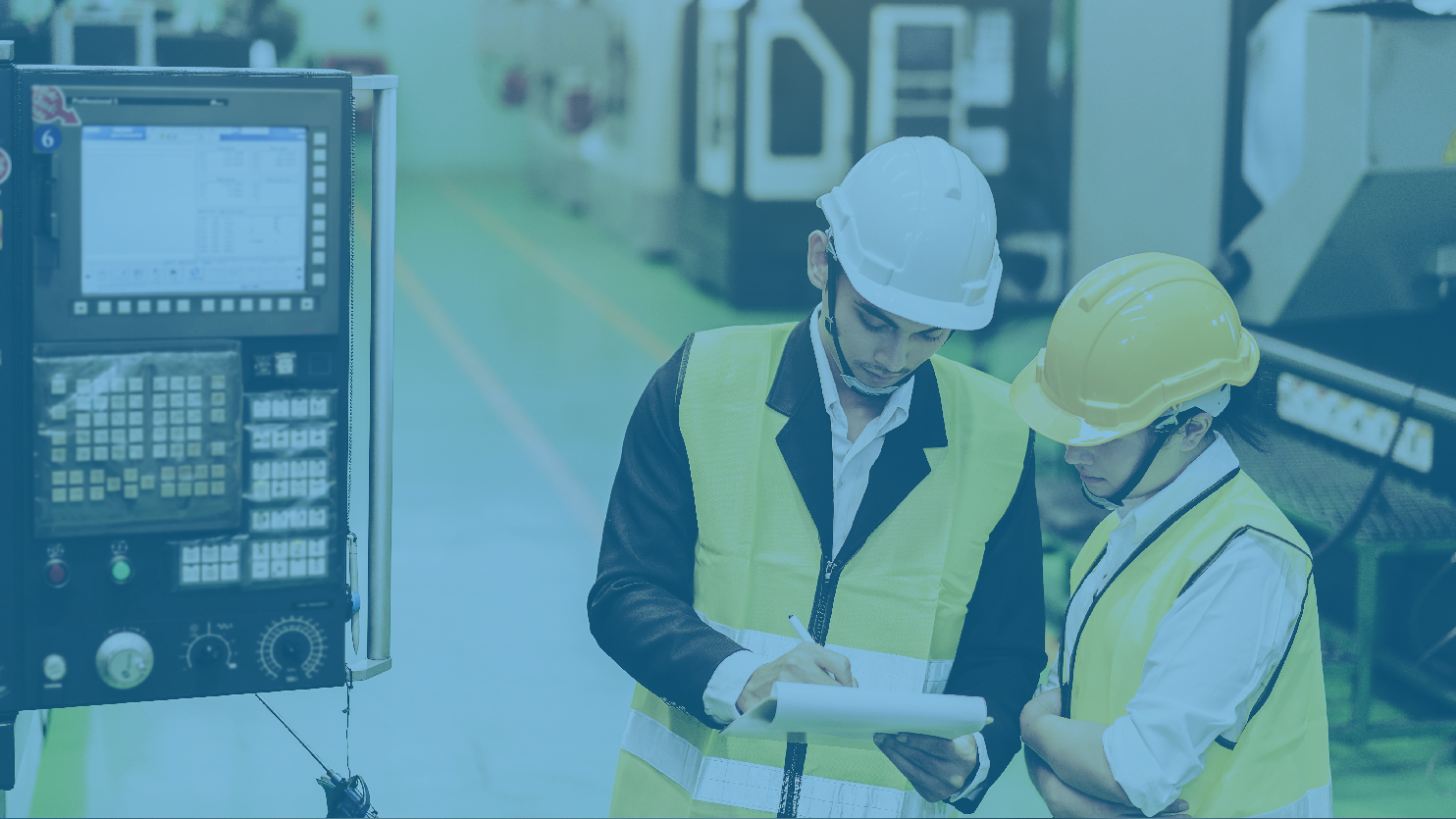
There is always room for improvement, especially when it comes to plastic injection molding. Here are 6 simple tricks that you can implement in 2022 to improve your injection molding processes.
1. Document standard process sheets
Having a standard process at every start up brings the process back to the same starting point every time. This will instill discipline and discourage the wild west gun slinger mentality. It is very difficult to measure anything without a standard to measure against. Even if you know that the process is not fully optimized or if it doesn’t meet your expectations, documenting what and how to do things helps you measure improvements.
Another benefit is that a few technicians on the shop floor may be more than capable of starting up a mold and making good parts without a setup sheet, but can everyone?
2. Don’t block cavities
Ok, this is easier said than done, but coming up with a plan to minimize cavity blockage is a good start. This could involve investing in spare tooling components, investigating the root cause for the tool breaking, and training for setup personnel, technicians, and the tool room.
There are many reasons why this is important to do. First, if you have documented standard process sheets, you now will have to change settings when cavities are blocked. This then degrades the idea of a standard setup sheet. Secondly, is the efficiency and economic impact. Machines have to run longer to meet orders, and they will use more resin if the tool is a cold runner and regrind is not incorporated back into the mix.
3. Schedule material color changes in the correct order
If certain machines run multiple colors throughout the month, it can be very beneficial to try to schedule the colors to start with the lightest colors and change to a darker color each time. Ideally you would finish the month in the darkest color that machine will run. Why? Color contamination showing as black specs or streaks of the previous color is time-consuming, hard to find, and usually results in reject parts.
The cleaning of all the material handling equipment is also time-consuming and a little less forgiving if the next color is darker, especially if the two colors are the same resin. If a machine can be dedicated to the same resin, that is even better.
4. Don’t cheat on drying
When a material supplier says a material needs to be dried, it really does. Too often we try and skip this step or not dry it for the correct time. This means drying at the correct temperature and the correct time. Keep in mind that plastic resin can also be over-dried. This can show as an increase in viscosity, an additive loss or discoloration. If the material is not dried enough, it becomes very difficult to process, resulting in bad parts and tampering with the standard process settings to “fix” it.
The best way to know if you are drying properly is to use a moisture analyzer. Just because the dryer is hot, does not mean it is drying properly.
5. Don’t use steel tools on your molds
Too many times I have seen someone with the best intention grab a pair of steel pliers to pull a stuck part out of a mold. This causes serious tool damage. Yes, brass pliers and tools are more expensive, but nothing compared to the cost of repairing the mold. Ensure you have the right tools to work on the molds.
6. Take care of your platens
The new year is a good time to start taking care of your platens when changing molds. Over time, rust and all kinds of build up will accumulate on the platens. When molds are installed in the machines, sometimes the mold will hit the platens and create indentations or burrs. If this is left unchecked, it can build up enough to affect how the mold is receiving the applied tonnage.
A 4-inch dual grit axe sharpening stone, a rag, and some WD40 are what you need to get started. Cleaning the platen with a rag and WD40, then using the WD40 and the stone will start removing the rust build up and true up the platen again. This also needs to be done on the clamp plates of the mold. Taking 5 minutes at each mold change to do this is a good habit.
Check out this video to see how to properly clean your platens.
Conclusion
By implementing these 6 injection molding tricks, you can be on the way to making higher quality parts, reducing costs, lowering waste, and reducing mold damage. Want to learn more how to improve your processes? We’re here to help! Contact us with any questions you have.